Според намерено скорост на рязане определя изчислява скоростта на брой shpindelyan (об / мин) с формулата:
където D - диаметър на детайла, мм.
След това изберете най-близкия по-малък или равен брой обороти н на машината на паспорт машината. Броят на оборотите на машината зависи от броя на скорости: за винт винторезни 1K62 модел се определя от Фигура 4.1.
Фигура 4.1 - скорост Графика винт винторезни
Ние се определи действителната скорост на рязане
при което - действителната скорост на рязане, м / мин.
В допълнителни изчисления с помощта на действителната скорост на рязане и броя на оборотите на паспорта на машината.
RezaniyaP сила (Н) обикновено се разпространява върху компонентите на сила, насочени по осите на машината координират (тангенциален Pz. Радиално и аксиално Ру Px).
Компонентите на силата на рязане се изчислява, както следва:
където - коефициент, отразяващ материал трябва да се лекува и материала на режещия инструмент;
- дълбочина на рязане, mm;
- действителната скорост на рязане, м / мин;
х. , N - експоненти.
На практика, изчисляването се извършва за тангенциалната съставна на режещите сили, които имат най-висока стойност. Средните стойности на коефициента и експонати х. , п за тангенциален компонент на PZ режещата сила е показано в Таблица 4.4.
Таблица 4.4 - Стойности на коефициент и експонати
във формулата за определяне на тангенциална режеща сила на PZ
Външната надлъжната Диаметърът
RezaniyaN мощност (кВт), изчислена по формулата:
Идентифициране на нуждите на електрическата енергия на машината
където - силата на машината, кВт;
- ефективността на задвижването на машината, която е в границите от 0.8 до 0.9.
Ако се окаже, че силата, необходима за завъртане на двигателя над машината мощност (машина за 1K62 elektrodvigakVt мощност), намаляване на рязане стойността сила чрез увеличаване на потока и да намали дълбочината на рязане, както и изчисляване на новите параметри.
Определяне на въртящия момент. изисквания за изпълнението на процеса на рязане
Определя вретено въртящ момент
Сравнете стойността на въртящия момент, предоставена от машината, с въртящ момент, необходимостта от рязане. Ако стойността на Mk. Чл. <Мк..р. то необходимо уменьшить силу резания. Целесообразно уменьшать силу резания за счет увеличения подачи и уменьшения глубины резания, соблюдая условие
Определя основния (технологични) Време (мин) от формула
при което - изчислена дължина на повърхността на лечение, mm;
5 КОНЦЕПЦИЯ ЗА технологичен дизайн
дизайн Workability продукт - сложен комплекс характеристики, което се определя от техническите и икономическите фактори на метод за производство на тази част. Най-важните параметри са материал консумация, сложността и разходите за производство [9, 13]. Обикновено се сравняват два или повече части на възможности за производство, като се вземат предвид специфичните условия на производство: Тип на производство - единични или серийни, наличието на производствената база - леене, заваряване райони, на районите на механична обработка, и т.н. ...
Използването като заготовки, стомана и чугун, серпентина и високи валцувани профили. За един елемент се препоръчва производство за получаване на преформа и инжекционно формоване членове на единични форма или заваряване детайли, изработени от стомана. За масово производство и обработка масова употреба налягане е най-ефективен, когато се повишава възпроизводимостта на подобен размер и характеристики на части се увеличава.
За оценка на използването на производството използване материал, материал, който показва количеството на празен материал, използван в частите, и се изчислява по формулата:
където mdet - много подробно в чертежа, в килограми;
mzag - тегло на детайла, кг.
Стойността на този коефициент е в диапазона от 0 до 1. Колкото по-близо до 1 стойността, толкова по-ефективно на материала, използван в статията (с други думи, по-малко материал отиде в чипове). Най-високата стойност на коефициента на използване на материала (1) предоставя методи за формоване, без допълнително обработване, когато заготовката обем, равен на обема на крайния част. При използване на сплескани за производството на различни части за машини за обработване на остатъка представляват 10 до 40%, докато степента на използване на материала е от 0,6 до 0,9, което означава, рационално използване на материала. При производството на отливки с последващо стойност обработка KISP. обикновено по-ниска, отколкото при използване валцувани заготовки и, освен това, материалът се консумира в системата на бегач, който може да бъде пренебрегнат, тъй като леяци се топят и се връщат към следващата запълване. Производство на продукти чрез заваряване осигурява фактор Матер голямо натоварване.
Въпреки това, количеството на материала фактор използване не позволява да се направи оценка на сложността на избрания метод за производство. За обективна оценка, изчислена стойност на производството на всяка избрана опция. Приблизителен сравнителна оценка на сложността може да се направи от броя на части от оборудването или области, които участват в производството на този продукт.
При сравняване на най-предпочитаното изпълнение трябва да се разглежда като тези производствени методи, при които се изисква материал стойност използване на около 0.7 или по-висока за обработка Апаратура и оборудване заваряване. тъй като тези области са на разположение за почти всяка индустрия. Обикновено лечението налягане осигурява по-добро използване на материята, но изисква специални скъпи матрици. Поради това, при липсата на производствената част формира почине, готов да този метод трябва да се предпочете да се хвърли в един вид.
ИЗЧИСЛЯВАНЕ ПРИМЕР 6 ИЗМЕРВАНЕ НА заготовки и подбор
Рационален начин ПРОИЗВОДСТВО ПОДРОБНОСТИ
Задача. На Фигура 6.1 рисунка на готовия част и изгледа му перспектива. Материалните Подробности - Cm 3 (мека стомана). изисква:
а) избиране на машинни квоти и за изчисляване на размерите на детайла да се получи част е показано на фигурата, чрез леене; изберете отливка с форма на позицията; изчисляване на елементите на системата за пропускане;
б) изчисляване на размерите и изберете преформа за производство на компонент, показано на фигурата, метод за обработка под налягане;
в) вземат заготовката за производство на частта е показано на фигурата, методът за заваряване;
Z) изчислено условия за рязане в превръщането на споменатата повърхност, с прибавка за обработване на (а);
г) оценка на техническите и икономическите показатели на производствените части, показани на фигурата, чрез леене, заваряване, пресоване и механична обработка, и да изберете най-ефективния начин.
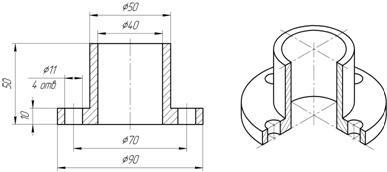
Фигура 6.1 - монтаж
6.1 Избор на квоти, за изчисляване на леене размери заготовки
и параметри наливните системи
Това празно могат да бъдат произведени чрез инжектиране в земята, с оглед на икономия на метал, за да се създаде централен отвор Ø40 е целесъобразно да се използва тоягата и отвори за закрепване на болтове O11 производство пробиване. От кастинга не предвижда предварително определена точност на размерите и чистотата на повърхностите след почистване на кастинга да бъдат обработвани на струг, за която трябва да бъде предоставена помощ за всички третирани повърхности.
За целите на квоти трябва да избере позицията на отливката във формата и повърхността раздяла на препоръките, дадени в литературата [4] и точка 1. Този елемент има проста конфигурация, и може да бъде всяка позиция (например, както е показано на фигура 6.1, цялата елемент се поставя в половината плесен). За симетрични части от повърхността на тялото на вид революция конектор Препоръчително е да поставите по оста на симетрия - с оформянето изисква само един модел, представляващ половината от отливката.
раздяла повърхност да бъде хоризонтална, така че елементът ще се намира във формата, както е показано на фигура 6.2.
Изборът квоти за обработка лята стомана съгласно таблица 1.2:
- в диаметрален размер Ø40 повърхности, Ø50 и Ø90, които са разположени чрез изливане отгоре, отстрани и на дъното, да симетричен голямото помощ - 3.5 mm (което е вътре надбавката за Ø40);
- на крайните повърхности части разположен отстрани чрез изливане, приема помощ до 3 мм.
За да може да се моделира вдлъбнатините без унищожаване на формата, необходима за осигуряване на отклонения формоване върху вертикални повърхности на отливката. Според приетите препоръки за Ø57 и Ø97 завършва наклон 0º45 ". Според препоръките за предотвратяване на вътрешни напрежения изисква плавен преход от дебелина на тънка стена, за тази цел извършване на наклон и радиус закръгляване R3 две перпендикулярни повърхности.
Скица на детайла с квоти, отливки оформени позиция и повърхност форма съединителя е показано на фигура 6.2.
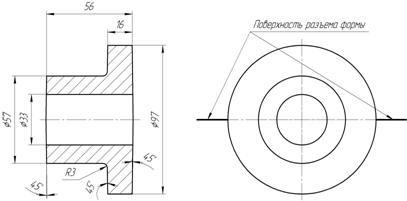
Фигура 6.2 - скица на детайла и позицията под формата на отливки
По скица определи обема и масата на отливката.
За да се определи обемът на кастинга за да се раздели на елементарни геометрични фигури (в нашия случай - на цилиндрите). При изчисляване на обема на наклони и радиуси филе пренебрегвани заради малката стойност на обема на тези компоненти.
където V1. V2. V3 - символи обеми Ø57, Ø97 цилиндри
и O33, съответно.
леене маса се определя с израза:
където # 961; - леене на метал плътност, определена от директорията. (За стомана # 961; = 7800 кг / м3 за желязо # 961; = 7000килограма / m3).
Изчисляването на елементите на леяковата система [4].
Маса хвърляйки бегач и печалбата се определя приблизително от препоръките, тъй като точните размери на тези елементи са все още неизвестни. Според препоръките (виж 1.1.), Маса бегач система за леене на стомана е от 60 до 80% от теглото на леене. Ние приемаме 70%. След това:
Маса бегач система леене с
Продължителност леярската форма се определя от формула (1.6).
Се приема за 1,5.
Средната дебелина на = леярските стени (57-33) / 2 = 12 (mm).
Определяне на общото напречно сечение на хранилки (1.7)
на плавността на коефициент на корекция на мека стомана приемам = 0.97.
Коефициент на изливане скоростта на леене се определя относителната плътност. Обем форма колебливо определи предварително определено допустимо разстояние за масата леене до 5 кг на топ модели на върха на колбата до 40 mm от дъното на модела на дъното на колба - 40 mm, от модела на стените на колбата - 30 мм. след това
сечение на плъзгачите ще
Площта на останалите елементи на системата за бегач се определя от уравнение (1.5):
сечение shlakoulovitelya
сечение на първата вертикална тръба (mm2).
6.2 Изчисляване и избор на заготовки за производството на части
метод Формиране
Определя добавки за обработка на детайла, получени от пластмаса работен [9]. Приблизителните стойности на обработка квоти на външните цилиндрични повърхности избират от таблица 2.1, в краищата на обработката - съгласно Таблица 2.2. Стойностите правят дълго квоти 4 Ø50 mm до 40 mm, 5.5 mm до 10 mm в дължина Ø90; на надбавката за крайните повърхности на 0.8 mm в Ø90, 0,7 mm при Ø50.
С оглед на помощ определят външните размери на заготовката:
диаметри от 50 + 4 = 54 (mm); 90 + 5,5 = 95,5 (mm);
дължина 10 + 0,8 + 0,8 = 11,6 (mm); 50 + 0,8 + 0,7 = 51,5 (mm).
Избор на заготовка за оформяне ще извършва, като се вземат предвид размерите, получени от стандартния брой студена кръг стомана (вж. Таблица 2.3). Най-добре на пръчка с диаметър от 55 мм и 95 мм.
За избор на звук заготовката на разглеждане на възможни методи на производство, показан на Фигура 6.1 части от валцовани:
1) като заготовката да изберете прът 95 мм в диаметър (с рязане на машинни квоти) мелене струг външна повърхност с предварително определени размери, пробиване вътрешния отвор и длето с диаметър от 40 mm, след пробиване машина за изпълнение на 4 дупки с диаметър 11 mm;
2) като диаметъра на преформа прът може да бъде избран 55 mm, изпълни разтоварване до образуване на локална диаметър сгъстяване 95 mm и предварително определена височина, за да квоти за превръщането на струг, централния отвор производство и болтови отвори, както и в предишния метод;
3) извършва разтоварване преформа диаметър на пръта на 55 mm, както и в предишния метод, а след това - на фърмуера централния отвор 40 мм в диаметър, последвано от третиране на външните повърхности на струг и производство на болтове отворите на свредлото.
При анализа на предложените методи за производство на части с помощта на лечение налягане, ние се отбележи следното. Първият метод е най-лесно да се извърши и разпространени в практиката изисква само механична част (струг и бормашина). Въпреки това, повечето от метала по време на това отиде в чипове, т. Е. Ще бъде нисък коефициент на използване на материала. Вторият метод над първия участък допълнително изисква наличието на гореща обработка и създаване на печат, но има по-висока материал използване. Третият метод е най-високата използване фактор на материала, но изисква прибавянето на първата и втората операция затворен EEPROM, което усложнява производствения процес и увеличава цената на едно парче с тънка дебелина на стената от 5 mm.
По този начин, като най-простият и най-рационалния начин да се избере второто третиране налягане, т.е.. Д. Кацане празно диаметър от 55 мм в диаметър 95.5 mm, последвано от обработка и пробиване централен отвор. Скица на детайла в резултат от разтоварването, е показана на Фигура 6.3.
За да се извърши този метод е необходимо да се определи количеството и дължината на заготовката утаява [16].
Обем засадени част на детайла се определя от формула (2.2):
в който обемът на коване определи скицата:
свиването на обема се приема равно на 1,5%, т.т.. д.
метал загуба при накаляване 0,5% с електрически преформа обем на нагряване:
Като се има предвид свиването и горят без да се излиза предоставяне чеп за да определи обема на формата засадени:
Свързани статии