Суровините - руда, агломерат, кокс, варовик и - след зареждане в доменната пещ, потапяне, изложени на насрещното потока на горещите газове намалява покачването от огнището на гърлото. В реакцията на суровини газове е непрекъсната промяна в температурата, химическия състав и физическо състояние на материала и съответно се променя състава, температурата и налягането на газ.
зареждане движение материал колона причинена от изгаряне на кокс от дюзата, абразия, смилане и стапяне на материалите и периодично освобождаване на желязо и шлака.
материали за понижаване на скоростта в пещта се различават както в хоризонтален разрез, а височината: най-високите скорости - над коксовите горивни зони, руда част от такса, особено след стопилката се движи много по-бързо (около два пъти) кокс. Времето за престой на материали в пещта обикновено е 6-8 часа. и средната скорост на 2.5-3.5 м / час. В горната част на скоростта на зареждане на пещта е 10 м / час, в средната част на шахтата се намалява до 5,4 м / час и на дъното (преди дюзата) - до 3,5 м / час.
Постепенно потъване пробивът материали влизат в пещта, зоната на окисление, където кокс изгарянето и частично окисление на преди това образувания желязо.
В планински движение на материали, кокс, е сложна. Метод кокс горене в дюзите в окислителна зона, съгласно представя изглед, подобен на изгаряне на гориво в леглото.
В близост до устието на реакцията на практика се случва
C + O2 = CO2; # 916; F ° = -94,200 - 0,2 Т.
Тъй като разстоянието от дюзата с увеличаване на интензивността на въглерод настъпва реакция газификация:
СО2 + С = 2CO; # 916; F ° = 40800 - 41,70 T
следователно се променя съставът на фазата на оста на копия (фиг. 8) газ.
Според последните доклади, подобен модел на промяна на състава на газа се наблюдава при малък брой от взрив. С нарастване на интензивността на топенето на качествено промяна на характера на горене. Преди дюзи енергично циркулиращ кокс и газ в сферична кухина, образувана от излизащи реактивната струя формите за вдухване (фиг. 9). Газификация на въглерод, докато тече в междинния слой околната потока сфера. Промяна на състава на газа в оста на практика в този случай има малко по-различен характер (фиг. 9) и се характеризира с относително малка промяна в концентрацията на кислород в зоната на циркулация.
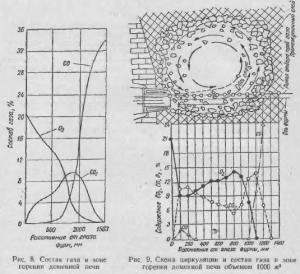
Образувани по време на процеса на изгаряне газове се разпределят през напречното сечение на пещта и да се премести през колоната на зареждания материал до гърлото. Поради заряд материали и форми, в зависимост от профила на разпределението на пещта газовия поток на хетерогенност пост е обикновено по-равномерно разработен периферна газов поток.
Времето за престой на газовете в пещта, 2-4 секунди. Най-високата скорост на газа се наблюдава на мястото на тръбата - за пара (до 32-64 m / sekmenshaya (22-24 м / сек) - зоната на пара -. При преминаване през заряд материали гърлото стълб постепенно намалява налягане и температура, както и промените в състава на газ ( Фиг. 10).
Диференциално налягане газ в пещта с повишено налягане на банкомата гърлото 0.7-0.75 е 1,1-1,2 атм. Максималната температура на 1800-1900 ° развиват в зоната на горене. Температурата на газа в горната част на пещта в топене на чугун е обикновено 200-300 °, над напречното сечение на температурата на пещта газ остава постоянно - стените на пещта е значително по-висока (Фигура 10).
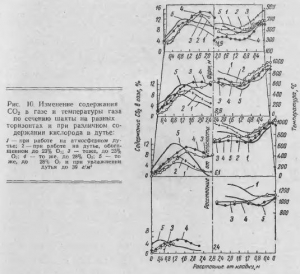
Чрез регулиране на пещта се наблюдава неравномерно разпределение на температурата, която носи S-форма. Най-явните промени в температурата на горните и долните зони и е относително слаб - в центъра. Според теорията на BI Kitaeva подобно разпределение на температурата определя от наличието на термални зони, в които топлообмен е практически завърши. В зоната долния пренос на топлина протича много активно и температура на газа бързо пада до температурата на обвинението; в средната зона на значителна разлика във височината на температурата е малък и няма почти никакво топлообмен; в горната част, която получава свеж заряд, в присъствието на голяма температурна разлика между газ и топлинна енергия постъпленията от пакета доста бързо.
Състав в подходящ състав газ копия подава към доменната пещ. При по-високи хоризонти първия газ, обогатен CO (до 37-41%) и след това СО2. Промяната в състав газ (фиг. 10) се появява като резултат от реакции на разпадане на редукция и топене материали, главно варовик.
Промяна в състава на суровините
След зареждане в доменната пещ от суровините под действието на горещи газове хигроскопична влага се отстранява и след това с вода на хидратиране. Отстраняването на водата на хидратиране обикновено завършва при 400-600 °.
Както се движат материали в зони с висока температура летливите вещества се отстраняват от кокса разлагат карбонати, понякога присъства в рудата, и варовик се разлага.
СаСО3 = СаО + СО2; # 916; F ° = 42490 - 37.7 Т.
Интензивно варовик разлагане се наблюдава при температури над 900 °, когато се освобождава налягане CO2 над атмосферното. Завършва разширяването, особено в по-големи парчета, при 1000-1100 ° С. На разлагане на варовик често изразходват до 15% от общото количество топлина. За да се запазят топлина и кокс консумация използва разредени агломериране висока алкалност; докато варовик от взрива на правилото за заплащане.
Намаляване на железни оксиди и други елементи
В основата на процесите на доменни пещи включва намаляване на оксиди на желязо. Намаляване на железни оксиди в твърдо състояние при условията на доменната пещ са предимно въглероден окис и в по-малка степен - водород.
Съвременната теория за намаляване на оксиди на металите на базата на купища съветски учени AA Байкова, М.А. Павлов, IA Соколова и сътр.
В съответствие с принципа на последователно преобразуване монтиран AA Байков, намаляване на железни оксиди се извършва в стъпки от най-високата към най-ниската до образуването на метално желязо.
При температури над 570 ° намаляване на железни оксиди от окис протича въглеродни съгласно следните реакции, по-долу реакции "индиректен" Възстановяване:
3Fe2O3 + CO = 2Fe3O4 + СО2;
# 916; F = ° -7880 - 12,87 Т;
Fe3O4 + CO = 3FeO + СО2;
# 916; F ° = 7,120 - 9,15 Т;
FeO + CO = Fe + СО2;
# 916; F ° = - 5.80 + 5,450 Т;
Под 570 ° магнитен железен оксид се редуцира до метално желязо директно, заобикаляйки втория етап.
Равновесие състояние за всяка от горните реакции се характеризира с равновесната константа Кр = pCO2 / рСОг, т. Е определен състав на газовата фаза при дадена температура (фиг. 11). Възстановяването е по-успешен от по-богати на газовата фаза на въглероден окис по отношение на неговото равновесие съдържание.
доменната пещ е намаляване на газовата фаза за всички железни оксиди [(pCO2 / рСОг) dom.pechi <<(рСО2/рСО)равнов], поэтому на любом горизонте печи имеются благоприятные условия для восстановления окислов железа.
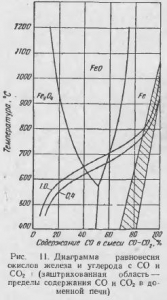
Също газова фаза обогатена на въглероден окис, успешно възстановяване на железни оксиди се насърчава от високи температури, достатъчно газ пропускливост на заряда, внимателно получаване на изходни материали и други фактори.
Механизмът на намаляване на окисите на желязо процес, съгласно теорията Chufarova GI и др. Е адсорбционна-автокаталитично. Процесът на възстановяване се намалява до три серийни етапа на адсорбция на редуциращия газ върху повърхността на оксид, реакцията на повърхност с адсорбираните молекули на редуциращ агент с кислород на оксид кристална решетка, придружени от кристални химични трансформации и десорбция на газообразни реакционни продукти.
В условията на намаляване доменна пещ на железни оксиди се случва с достатъчна скорост и започва в горните хоризонти на пещта. Железният оксид се отделя при 350-400 °, FegO4 - в интервала от 600-800 °. Възстановяване на железен оксид настъпва при още по-високи температури, а от 950-1000 ° и по-високо извличане на железен оксид потоци, включващи горещи кокс въглерод.
Така нареченият "пряка" възстановяване
FeO + С = Fe + СО; # 916; F ° = 35350 - 35,9 T
настъпва действително редуциращ газ - въглероден окис, генерирани от взаимодействието
СО2 + С = 2CO; # 916; F ° = 40800 - 41,70 Т.
По този начин, пряко намаляване настъпи едновременно реакция FeO намаляване на въглеродния монооксид и взаимодействие CO2 с въглерод. Скоростта на този процес се определя главно скорост на реакцията въглероден газификация. Температурата на само зоната на директна редукция лежи над 1100-1200 °, утаяване в BOSH и пара.
Директно от конвенционалните сортове в топенето на желязо е намалена 40- 60% желязо. Намаляването на степента на директна редукция помага за намаляване на потреблението на кокс.
За всеки клас на желязо и различни условия на топене трябва да съществува оптимално съотношение между преки и косвени реставрация. За подобряване на техническите и икономическите параметри на топене е необходимо да се увеличи степента на непряко намаление постига внимателна подготовка на суровини и по-добро разпределение на газовете в пещта и други дейности, които увеличават reducibility на таксата.
Освен въглероден окис, газовата фаза на доменната пещ в малко количество (1.6-2.6%) съдържа по-енергични редуктор - водород, което ускорява намаляването на оксиди на желязо.
Наред с железни оксиди свободни в агломерати, рудата и шлаката се добавя към партида, обикновено присъства желязо силикат съединение. железни силикати са оформени в доменната пещ и в образуването на шлака. Възстановяването е по-трудно да се желязо на тези съединения; тя идва от фазата на шлака от въглерод в BOSH и раменете. Този процес се улеснява чрез добавяне на вар в заряд поради образуването на твърди калциеви силикати,
2FeO * SiO2 + 2С 2CaO + = 2Fe + 2CaO * SiO2 + 2CO;
# 916; F ° = + 51 700 - 76.5 Т.
В допълнение към желязо в доменната пещ се намалява определено количество силиций, манган, Р и в някои случаи, Cu, Ni, Cr, Както и други елементи. Тези елементи като оксиди, или други съединения, или са в проникване материал, или те са въведени в заряд (например, Mn) до получаване на желания състав на желязо. възстановяване на теглото на тези елементи зависи от условията на температурата на топене, силата на оксид елемент, състава и свойствата на шлаката, възможността за образуване на разтвори с желязо и карбиди, и други фактори. Trudnovosstanovimye оксиди МпОг и SiO2 се възстановява в висока температура зона (в BOSH и огнището) въглероден предимно шлака:
Когато чугун топене пристъпи към метал заряд 50-70% манган в количество по-голямо от това се намалява при топенето на високо-манганов чугун; възстановява силициев много по-малко количество (25-35%), по-голямата част от него остава в шлаката. Фосфорът е почти напълно възстановен и се прехвърля в желязото само на топене ферофосфорите 5-12% P отива в шлаката. възстановяване на фосфор е чрез директно в по-ниските хоризонти на вала и задушени чрез взаимодействие
(СаО) 3 * P2O6 + 5 ° = + CJSIC 2P + 5Co
2 / 5P2O5 + 2С = 4 / 5P + 2CO; # 916; F ° = 94600 - 91,27 Т.
От другите елементи в доменна пещ в присъствието на тях в суровината е почти напълно възстановена мед, никел, кобалт и повечето от хром.
Образуването на желязо и шлака
Руда процес намаляване завършва образуването на метално желязо. Частиците на редуцирано желязо рудата или отделна част агломерират смесват с скалата на отпадъци, под формата на гъба. Постепенно отпадане, те са изложени на по намаляване на газ на все по-високи температури. Метално желязо газо- навъглеродените и скални примеси, взаимодейства с ненамалените железни оксиди и манган, както и вар, образува първичната шлака (фиг. 12). Цементация твърдо желязо, както изглежда, е в съответствие с реакции:
2CO = СО2Н-С; # 916; F ° = - 40 800 + 41,77 ";
3Fey + С = FESC; # 916; F ° = 2,475 - 2,43 Т;
3Fey + 2CO = Fe3C + СО2; # 916; F ° = - 38 325 + 39,27 Т.
За да се определи оптималното количество на бази в шлаката в топилна желязо кокс от различни класове се използва като формула AN Рам
Най-важните физичните свойства на точката на топене на шлаката и вискозитета разтопими шлаки имат температура на топене 1250-1300 °, огнеупорни - до 1540 °. Вискозитетът на стопилката кокс шлака при 1500 ° PZ е 2-10. Повечето от основните токсини са течности, тези, в които съотношението на SiO2 + Al2O3 / СаО е близък до единица.
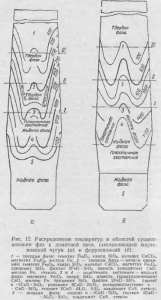
Сярата се въвежда в доменната пещ предимно кокс и в по-малка степен - на рудата и варовик. Зареждането на доменната пещ съдържа приблизително 9,8 кг сяра на 1 тон чугун. По време на горене на сяра се окислява кокс образува SO2 и H2S частично възстановен въглерод-сяра пара. Малка част от пара сяра се пренасят от газ, повечето от метал става. Желязо сяра се отстранява чрез взаимодействие с шлаката главно чрез реакция в огнището на доменната пещ
FeS + СаО = CAS + FeO; # 916; F ° = - 430 - 0,16 T
FeO + C (Si, Мп) = Fe + CO (SiO2, МпОг)
Vnedomennaya сероочистваща
След освобождаването от доменната пещ в разливна кофа и гласове при ниски температури миксер има отстраняване частично сяра резултат от екзотермичната реакция
FeS + Мп = Fe + MnS; # 916; F ° = - 35 010 + 8,46 T
Степента на десулфуризация манган малък и зависи от първоначалното съдържание на манган и сяра в желязото. Следователно прибегне до други, по-ефективни методи за десулфуриране кофата например за обработка на желязо алкален сода каустик и солна калциниран. Операция се извършва обикновено в горещ метал черпак. Десулфуриране сода се дължи на образуването на общите реакционни Na2S
FeS + Na2CO3 + 2С = Na2S + Fe + 3SO
Степента на десулфуриране може да бъде 70-90%. Въпреки че този метод е широко разпространена, неудобството на прилагане на алкален, високо износване на огнеупорни материали, намалена процес ефективност при отстраняване на отлагане на калцинирана сода и други недостатъци ограничи неговото по-нататъшно развитие.
За десулфуризация прилага също твърди реактиви на основата на калций -. Печена вар, варовик, калциев карбид, калциев цианамид, и т.н. В основата на този метод е реакцията на
FeS + СаО = CAS + FeO
Свързани статии