Практика и перспективи на защитно покритие върху тялото части и компоненти потопяеми центробежни помпи
Жилищните части и компоненти на потопяеми центробежни помпи са постоянно изложени на механично отстраняване на примеси, за образуване на течности разрушителна дейност, високо съдържание на вода, мащабиране, висока температура и образуването на галванични двойки. Всичко това води до унищожаването на електрохимична корозия на материали (вж. "Корозия унищожаване ESP"). Поради продължаващото влошаване на депозитите на петрола на корозионните проблеми се задълбочават непрекъснато, което изисква усъвършенствани методи за повишаване на устойчивостта на износване и корозия свойства ESP възли.
Днес компании използват различни методи за защита от корозия: въвеждане на инхибитори на течност формация, подмяна на материали и компоненти с нови, прилагането на защитни покрития и импрегниране. Най-популярните и ефективни анти-корозионни агенти са метални и жертвен слой, и подобряване на тяхното действително посока подава оптимизация състав, структура и технология покритие.
Днес, проблемът на корозия унищожаване на телесни части и възли, потопяема центробежна помпа е решен чрез различни методи.
Първо, въвеждане на инхибитори на образуване на течност корозия, които насърчават пасивиране на металната повърхност на родителя възли ESP, т.е. образуването на оксид филм тънък, предотвратяване на разрушаването на основния материал.
На второ място, замяна на материалите и компонентите на части от тялото на нови материали с по-висока устойчивост на корозия ESP.
На трето място, прилагането на устойчиви на корозия на метални покрития чрез високоскоростен пламък пръскане на основата на желязо. Използването на легиращи елементи в депозираните материали се увеличава устойчивост на износване и устойчивост на корозия, дава възможност за намаляване на порьозността, което води до повишаване на якостните свойства на материалите и минимизиране на корозия podplenochnuyu.
На четвърто място, прилагането на метални антикорозионни покрития с дъга пръскане. По този начин е налице значителна порьозност, което изисква дебелина вискозен импрегниране допълнителна защита.
Накрая, на пето място, като се използва импрегниране, включително, включваща флуор-съдържащ повърхностно активни вещества, които осигуряват допълнителна защита от корозия и защита на сянка зони.
Всички тези техники се използват за защита срещу корозия на ESP единици, имат свои собствени недостатъци. Например, инхибитори на корозията са ограничен период от време. Смяна на компоненти и части на тялото, ESP нов материал, като например неръждаема стомана, много скъпо събитие, което също оставя нерешен проблемът за корозия на корпуса и с нова. Импрегнители материали, които се използват в покритието за защита прилагат електрически обшивка, действа като щит топлина ESP възли, което води до прегряване на части, което влияе неблагоприятно на работата на цялата инсталация.
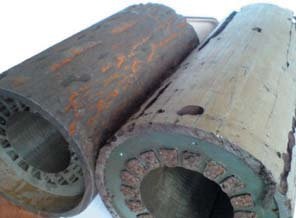
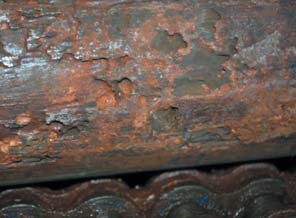
Схема електрохимичен процес при механично повреден метално покритие
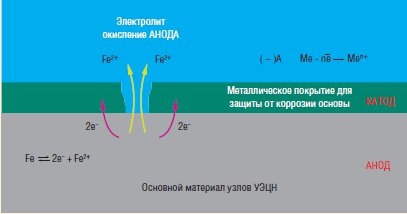
Защитно и покритие на метали на протектора
Отлага върху външните повърхности на частите на корпуса и събрания ESP метално покритие на базата на желязо с добавянето на легиращи елементи (хром, никел, силиций, молибден, бор и въглерод, които имат по-положителен потенциал електрод от потенциала на корпуса на неблагородни метали ESP) са добра защита от корозия но само толкова дълго, тъй като няма механични повреди на покритието. Ако се появи по време на инсталацията или ESP щети ACT, галванична двойка, образувана от: покритие на метала става катод по отношение на корпус, ESP - анод. Процесът на галванична корозия между покритието и материала на тялото, което води до корозия на защитеното podplenochnoy ESP корпус и корозия корпус.
В процеса на електрохимична корозия основното тяло материал се окислява, се разлагат в положително заредени йони в електролита - течност за образуване и електроните (виж "Схемата на процеса на електрохимична корозия в корпуса ESP с металното покритие е механично повреден.") Anodkorpus разтваря.
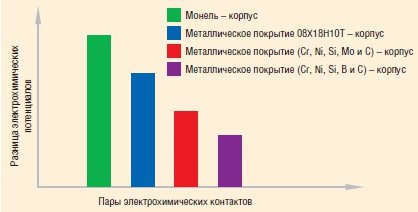
Излишните електрони вливат част катод - металното покритие.
За решаване на проблема на корозия podplenochnoy части на тялото и ESP единици обикновено се използва електрохимична защита. Това включва прилагане на протектора (анод) на капака (Al, Zn, Mg или техните сплави) върху метална имаща потенциал електрод повече отрицателно от потенциала на металното покритие, корпуса на ESP основен материал и корпуса (cm ". Разликата между електро-химични потенциал между корпуса и прилага защитни покрития "). Въпреки това, в случай на механични повреди по време на монтажа ESP корпуси започва галванична корозия между протектора и металното покритие (cm ". Схемата на процеса на електрохимична корозия в корпуса ESP когато механично повреден и метални покрития протектора").
Ако покритието е счупен, се образува галванична двойка между алуминия или цинково покритие, което става анода и металното покритие или ESP корпуса на неблагороден метал, който се превръща в катод по отношение на повърхността на протектора. В този процес, защитно покритие се разрушава при запазване на основните части на тялото материал и ESP възли на които се срещат процеси за редукция. И ръждата им ще започне след защитно покритие напълно prokorrodiruet.
Ритуални покрития на базата на цинков и алуминиеви сплави са устойчиви на морска вода за 10-60 години и имат ефект на "обрастване" пукнатини, драскотини. За сравнение, лакови покрития (LPC) осигуряват устойчивост на морска вода от не повече от три години, освен това, когато се използва в морска среда в микропорите развива бактерии, което води до образуване на локална корозия на корпуса стомана.
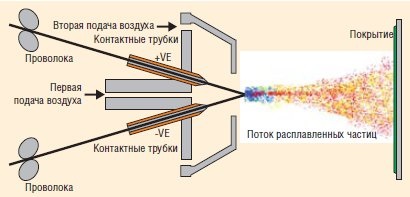
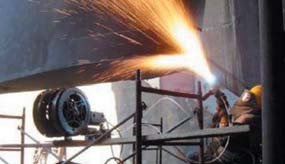
Схема електрохимичен процес корозия в корпуса ESP когато механично повреден и металното покритие на протектора
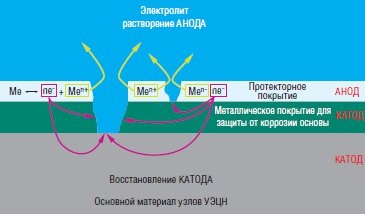
Висока скорост на разпрашване схема
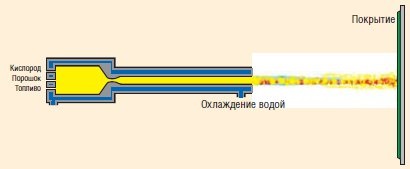
Днес метал и жертвени покрития са ефективни методи в борбата срещу корозия, както и един от най-важните направления за подобряване на състава действа, за да се оптимизира, структура и приложение на технологиите. Работата в тази област, проведено от няколко организации, по-специално "декомпенсирана" заедно с председателя и VNIIGAZ електрохимията MSU. Ломоносов. Тази работа ще избере най-подходящото покритие за всяко поле, като се вземат предвид характеристиките на неговото действие.
дъга пръскане
Газ термично пръскане (GTN) е процес на нагряване, дисперсия и трансфер на активираните частици разпръсква материал от газовия поток и образуването на компактен слой върху субстрата. За това покритие се прилага високо, плазма, пламък методи, методът на пламък настилка и дъга пръскане.
Arc метализация (. Cm "Схема дъга пръскане") дава възможност да се получат покрития върху големи площи, тъй като ефективното ефективността на пулверизатора достига 70-90% - най-високата сред методи ОБТ. С този метод са покрития на основата на Al, Zn, ZnAl, Cu, Fe. В момента пръскането на дъгата се използва за защита на оборудване, произведено от "борец" фабрики ", Новомет", "маслена помпа Service", "Alnas" и др.
Цинк alyuminievogopokrytiya ZnAl (85/15)
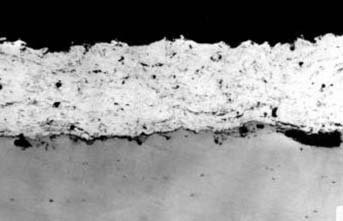
Алуминиева-магнезиев AlMg5 покритие
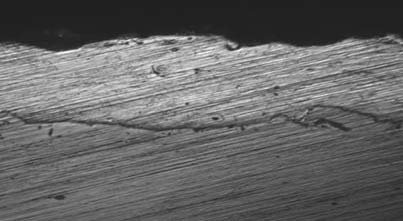
Електрически дъга спрей метализация използване монел и неръждаема стомана има якост на свързването на 15-35 МРа, порьозност - 5,10%, микротвърдост - 150-330 HV. Освен това, от неръждаема стомана, често се прилага на руски, докато Запад по-популярни monelnye покрития, които имат относително по-висока порьозност и следователно се нуждаят от специално импрегниране podplenochnoy за предотвратяване на корозия.
Електрически дъга спрей метализация се използва цинк, алуминий и техните сплави има лепило съдържание 70-80 МРа, порьозност - 10-20%, на микротвърдостта на - 35-50 HV (виж "Електрически дъга спрей метализация".).
HIGH SPEED SPRAY
Висока скорост на покритие включва използването на ултразвуков поток от материали, което позволява да се получат покрития с възможно най-високите термични методи спрей за адхезионни и кохезионните характеристики (см ". Схема високо отлагане"). Частиците на прах имат размер от 30-50 микрона. Такова покритие може да се разглежда като алтернатива на галванични покрития и вакуум методи.
пръскане с висока скорост се използва за възстановяване изхабен, както и втвърдяване на нови метални повърхности, които изискват висока износоустойчивост и плътност. Трябва да се отбележи, че тази технология не ни дава възможност да се защити вътрешната повърхност на тръбите, което би било приемливо за клиента от икономическа гледна точка.
Въпреки факта, че от страна на клиентите, чувствах интерес към тази технология са ефективни начини за намаляване на разходите за нея, за да приемлив икономическите резултати не се вижда. Днес, високоскоростен покритие се използва за защита на някои части на самолети пето поколение - за тази цел се използва високо-комплекс плазма инсталация, което позволява да слой на вътрешната повърхност на диаметъра на тръбата 60 см и дължина 1.5 m разходи покритие в този случай е 250 евро на квадратен дециметър .. Ако процесът по такъв начин 2Км вътрешната повърхност на тръбата, тръбата ще бъде почти злато.
Схема на топлинна спрей нанасяне на наноструктурирани покрития
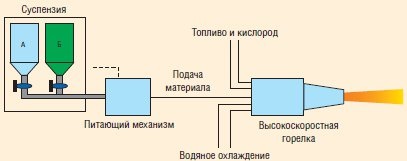
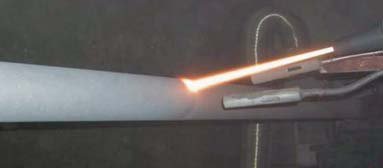
Приложеният метод на разпръскване високо корозия на сплави базирани на желязо има микротвърдост на HV 500-800 и силата на лепило на 70-80 МРа. сплави на никел-базирани имат порьозност от не повече от 2%, на микротвърдостта от - до 820 HV, адхезивната сила - 70-80 МРа. Порьозността на твърди сплави е също в рамките на 2% при HV и адхезия силата на микротвърдост 900-1200 по-голямо от 80 МРа.
Така, покритието депозиран с помощта на високоскоростен разпрашаване, са по-високи качествени характеристики в сравнение с тези, депозирани от електродъгова метализация (см. "Характеристики на методи покрития, използвани за защита на сгради ESP"). Особено важно е ниска порьозност, тъй като в този случай не се изисква допълнителна накисване.
Разходите покрития депозирани използване дъга пръскане, се дължи на по-голямо количество материал по-висока в сравнение с тези, депозирани от отлагане висока скорост. В същото оборудване, което се използва за отлагане с висока скорост, на стойност десет пъти по-скъпо оборудване за пръскане дъга.
Характеристики на методи покрития, използвани в защита ESP корпусите на