Тъй като този материал е предназначен за любители, че е необходимо да се говори за някои от етапите на производство на порцелан, които са много добре запознати с професионалисти, но остават извън полезрението на всички останали. Много колекционери и продавачи на порцелан никога не са били в производство и нямат необходимите знания.
Най-често задаваните въпроси са ми дали възможност да се разбере, че като цяло хората не разполагат с никакви възможности да се прости отговори, че не се нуждаят от потапяне в технологичната сложност.
Най-честият въпрос: Защо порцелан продукти са кухи отвътре?
Разбира се, въпросът се отнася до формите на скулптурата и ястие. Има плоски продукти, които са направени от формоване или пресоване и не са вътре в кухините.
Има процеси, които са по-добре да се покаже, отколкото да се обясни. За да започнете, аз препоръчвам да гледате кратък филм за производството на порцелан:
Течен кремообразна маса (порцелан приплъзване) се излива в определено време в пластир плесен. Гипс абсорбира влага за образуване на Shard на продукта. След дебелина глинен съд става достатъчно, оставайки под формата на суспензия се излива през изпускателния отвор. Дебелината на стената на продукта, в зависимост от обема си може да бъде 3 мм. до 8 мм.
Порцелан в производствения процес, и има горивна свиване на въздуха, т.е. пропорционално намалена в размер от 14-16% от оригиналния модел. (Снимка).
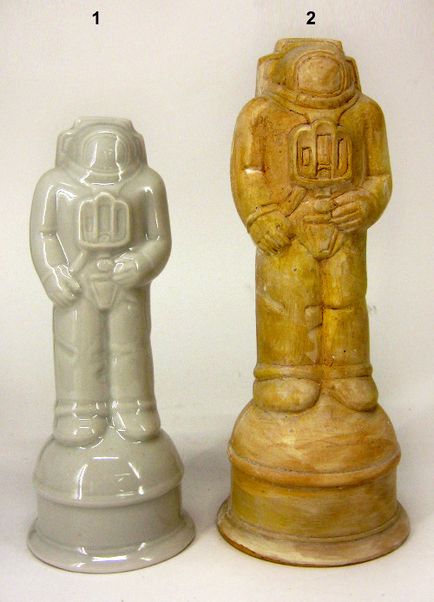
Температурата на 1350-1410 градуса полива порцелан стрелба. Процент на свиване варира в зависимост от температурата. Температурата на пещта камера може да бъде различен в зависимост от местоположението на пещта. В съответствие с това, че ще бъде различна и свиване. Свиването зависи от дебелината на стената (глинен съд) продукт. При по-дебели стената, по-свиване. Ако продуктът е отлята твърде дебели стени и да е непостоянно, дебелина на стената, когато се полива изпичане може да се случи на деформация на повърхността. Твърде слаб продукт все още до голяма степен деформирани Полити стрелба. Най брак порцелан проявява полива след изпичане: мухи, малки дупчици глазура pleshiny (prostuplenie матова глинен съд, в следствие глазура неравномерно дебелина), балони и т.н., и монтаж глазура Трябва да се каже, че процентът на дефект полива след изпичане може да бъде до 50% в размер на 15%.
В големи индустрии, контролирани от технологията на приготвяне суспензия от CPL. суспензия плътност е 1.72 грама на кубичен 1 cm. Плътността се измерва чрез хидрометър. Плътност 1,28 гр глазура. Glaze се отглеждат в големи резервоари, за които бихме могли свободно да се потопите напълно продукта. Когато изсъхнат, могат да образуват капчици и петна, които проби се отстраняват от продукта чрез филц. За да се получи продукта на степента на изпичане, дъното на напълно почистена от глазурата и се промива с влажна гъба. В пещ продукт се поставя върху плочата на силициев карбид, покрити с каолин. Каолин предпазва продукта от залепване към плаката по време на процеса на изпичане.
първо Utelny изпичане се извършва при температура до 900 градуса за фиксиране на гърнето и последващо остъкляване.
Процесите, които се провеждат по време на изпичане на порцелан, описан в литературата. При удар в електрически пещи има постепенно повишаване на температурата, която се показва на устройствата за контрол и евентуално изпитва при използване на керамични конуси, които имат предварително определена температура на топене. Конус с определена температура етикет кондензиран и се допира до горната част на основата, когато достигне желаната температура. Полива изпичане порцелан е по-добре да се произвеждат в газови пещи, което може да се постигне най-голям бял порцелан. Пещта газ се появява повече начини за смяна чрез подаването на въздух и корекцията газ. Възможна порцелан скорост изпичане, в която и изсушен продукт може да се нагрява при до 900 градуса в час в окислителна среда рязко с увеличаване на подаване на въздух. Когато бързо изгаряне на възстановителния период старт съответства на температура от 1000 градуса, в края на 1200 градуса (повишаване на дебита на газ). Освен повишаване на температурата идва в слабо намаляване атмосфера. Обикновено, всеки пещен газ, съставен оптимален график стрелба с индикатори на налягането предписаните газ и въздух. Опитните obzhigalschikov в крайна сметка се определи температурата в цвета на пещ пламък. При достигане на желаната температура се провежда в продължение на 15 минути, за да изравни температурата в целия обем на пещта, при което подаването на газ се спира. След това пещта чрез продухване с въздушно охлаждане. От 1350 до 900 градуса може бързо да се охлаждат. Освен това по-добро провеждане на естествено охлаждане, където фурната малко унищожени.
За онези читатели, които искат повече подробности за технологията на изпичане, давам един цитат от ръководството: "Полити изпичане може да се раздели на няколко периода, всеки от които се извършва при определени температури и контролирана атмосфера, което гарантира постепенното формиране на гърнето с необходимите качества.
първият период порцелан изпичане (20-950 ° С) се характеризира с различни физико-химични реакции, в зависимост от продуктите на предварителната подготовка полива калциниране и сушене на продукти след остъкляване. Предварителна подготовка зависи от степента определя от първата изпичане и присъствието в състава на продуктите от газообразни продукти.
Главно отстранява механично свързани и остатъчна вода е хигроскопична. И двата вида вода изпаряват при температура 110-130 ° С
След затопляне порцелан направи по-интензивно повишаването на температурата. В този температурен диапазон настъпва дехидратация окончателен глина материал и пълно отстраняване на химически свързано хидратна вода, ако процесът не е завършен през първото изпичане. Най-активният двойката разпределени хидратна вода в температурния интервал 500-600 ° С
Тъй като при тези температури порцелан все още достатъчно висока порьозност, влага бурно развитие през този период не води до напукване на продукти глинен съд. Furnace газ среда не оказва влияние върху премахването на водата от хидратация.
Приблизително температура от 200 до 500 ° С по време на изпичане на продукта се разтваря (адсорбирания), сажди от димните газове. Над 700 ° С започва постепенно прегаряне, което се случва по-активно в окислителна среда. Едновременно с това, сублимация на органичните вещества, съдържащи се в глинен материал, който също е придружено от цементация глинен съд. За да се намали цементационен статия в този температурен интервал се поддържа окислителна газова среда (= 2-4).
Не изгорена при достигане на 1000 ° С въглерод като остатъци не отстраняват влага, в по-късните етапи на синтероване допринасят за образуването на мехури в форма "петна" в резултат от затварянето на течната фаза, която започва да се образува при температура от 950 ° С, част от капиляри в калцинирания черепки ,
Не изгорял в началото на период на възстановяване парчето адсорбираното въглерод може да предизвика дефекти в следващите периоди порцелан изпичане, особено в първоначалния период на охлаждане, тъй като, след период на възстановяване, когато съотношението на СО: СО2 става по-малко от 0.1, е възможно да се образуват мехурчета изгаряне на газ, което води до появата на точкови отвори и порцелан kraterovidnyh вдлъбнатини.
Органичните материали, както и въглерод и адсорбираният, трябва да се отстранят напълно от върха на периода на възстановяване глинен съд рязко окисляване атмосфера с излишък на кислород (около 4-6%), тъй като при температури над 1050 ° С калциниране вече е проведено в редуцираща атмосфера ,
Необходимостта за изгаряне на органично вещество до температура от 950 ° С се дължи на факта, че при тази температура порцелан има достатъчно висока порьозност (проницаемост), улесняване безпрепятствено изходни газове, които се образуват по време на изгаряне на органични вещества. Продължителността на изгаряне на органични вещества от порцелан зависи от съдържанието му дебелина и кислород, както и клетките на звука.
През този период (при температура от 575 ° С) на реакционната калциниране реализация се осъществява? -kvartsa в? -kvarts, което е съпроводено с повишаване на обема на продукти, които, обаче, не предизвиква появата на дефекти. Причината за това е големият брой пори в порцелана на отопляем маса. Освен това, разширяване на повърхностните слоеве на продукта, имащи сили на натиск, че материалът е устойчив.
До температура от 1000 ° С краища декарбонизация (термично разлагане) магнезиев карбонат MgCO3 СаСО3 и калциев присъства в маса порцелан. MgCO3 магнезиев карбонат започва да се разлага при 650 ° С, и СаСО3 калциев карбонат - при 920 ° С
В такива относително ниски температури, материалът има по-голяма пропускливост на газ, който улеснява гладка изхода получен при разлагането на карбонатите, CO2 въглероден диоксид.
Вторият период на изпичане се осъществява при температура 950-1050 ° С в окисляване среда драстично. През този период, с изключение на реакцията завърши декарбонизиране и конверсия - -kvarts в настъпва интензивен въглерод прегаряне в Shard пълно освобождаване на материал от остатъците на хидратна вода, както и окисление на железни съединения.
Отоплителни продукти в втория период изпичане е почти изотермично природа, която насърчава изравняване на температурното поле в обема на продуктите клетки.
Третият период на изпичане - намаление. Периодът на възстановяване се създава увеличаване на концентрацията на СО в продуктите от горенето в температурния диапазон 1050-1250 ° С Въглероден моноксид CO възстановява железен оксид Fe2O3 до FeO оксид и калциев сулфат CaSO4 и Na2SO4 натриев - сулфит до сулфид и предотвратява изкълчване глинен съд и допринася за ефекта на "избелване" порцелан. Освен това, FeO благоприятства образуването на стъкловидното тяло (течна) фаза синтероване простира интервал. В стъкловидно фаза от своя страна допринася за интензивността на реакционната mullitoobrazovaniya (мулит - основният компонент на кристалната фаза порцелан).
Реакцията на редукция на железен оксид Fe2O3 до FeO извършва при следните схеми:
3Fe2O3 + CO = 2Fe3O4 + CO2
Fe3O4 + CO = 3FeO + CO2
O2 + 2CO = 2CO2
2FeO + SiO2 = 2FeO • SiO2
Повишаване на температурата по време на този период изпичане и СО концентрация ускорява реакцията, но твърде силен или твърде късно (в температура) по време на скоростта на възстановяване на образуването на стъкловиден фаза може да надвишава реакции за намаляване на скоростта и газове не намират изход глинен съд, предизвика образуването в нея на мехури. В стъкловидно фаза се образува предимно при температура 1150-1170 ° С, въпреки че малко количество от него се образува при температура 950-1000 ° С В маса порцелан съдържа други компоненти, отделят газове при нагряване, обаче, тези газове трябва да бъдат премахнати, за да се постигне температура от 1170 ° С, т.е.. Е. Преди топене фелдшпат, порцелан има друг, когато достатъчно газ пропускливост.
редукционна реакция на калциев сулфат CaSO4 и натриев Na2SO4 протича както следва:
CaSO4 + CO = CaSO3 + CO2
CaSO3 + CO = СаО + SO2 + CO2
Na2SO4 + CO = Na2SO3 + CO2
Na2SO3 + CO = Na2O + SO2 + CO2
Ако намаляване на околната среда в този период замени окислител, разлагането на сулфати завършва при температури по-високи от точката на топене на фелдшпат, което ще доведе до образуването на мехури. Намаляване среда значително намалява температурата на отделянето на газ тегло на компонентите, като по този начин получаване на дефекти (без мехури) глинен съд.
Продуктите на горене на СО могат да се съдържат в количество от 3 до 8%, в зависимост от вида на пещта. Увеличаването на съдържанието на СО е нежелателно, тъй като в този случай в продуктите от горенето образува саждите, което се нанася върху продукта. С допълнително я прегаряне може да се случи на дефекти глазура - малки дупчици.
Продължителността на периода на възстановяване се определя главно от дебелината и формата на калцинирания продукт.
Гледан температура от 1050-1250 ° С се придружава от интензивно свиване маса. Така капиляри и пори в глинен съд постепенно затворени и дифузията газ заглушават. Най-силен свиването се осъществява в температурния диапазон 1000-1200 ° С Най свиване съответства на най-печат на глинен съд.
Четвърти период изпичане (1250-1410 ° С) - синтероване порцелан - продължават по неутрална среда.
През този период, разширяването продължава алуминосиликати, съдържащи се в керамичната маса, от наличието оксиди с последващо образуване на мулит (3A12O3 • 2SiO2) и свободно силициев диоксид; Това завършва образуването на стъкловидни и кристални фази; синтероване порцелан, в която придобива основните физико-механични свойства и химическа устойчивост.
Този период продължава от температурата от 1250 ° С до крайната температура на синтероване, големината на които зависи от състава на масата на порцелан може да варира от 1280 (мека порцелан) до 1410 ° С (твърд порцелан). За да се получи желания микроструктурата характеризира със затворена порьозност от 2 до 4%, оптималната температура на калциниране се определя на 20-50 ° С над максималната температура на уплътнение. Повишаването на температурата над оптимума ще доведе прегаряне порцелан, в която бял се намалява, увеличава порьозността, сила намалява продукти.
Четвърти период забавяне изпичане завършва при максималната температура за времето, необходимо за завършване на реакцията синтероване, както и по-равномерно разпределение на кристалната фаза в стъкловидното тяло. Продължителността на експозицията зависи от количеството на калциниран продукти. Прекомерното излагане води до увеличаване на прегаряне продукти. Липсата на излагане на бързо повишаване на температурата от 1250 ° С до максимум създава непълни горивни продукти.
Пето изпичане период - закаляване. При охлаждане порцелан е много важен момент стъкловидното фазов преход от стопения към твърдата еластично състояние и втвърдяване точката на глазура.
Преход температура на твърдо състояние съответства на точката на втвърдяване на глазура върху Китай. В glazypey твърди маси тази температура точка е около 700 ° С, в меки порцелан глазури - 550 ° С За парчето между глазурата и термичните напрежения не се появяват, се препоръчва да се намали скоростта на охлаждане в тези температурни граници. В противен случай, това може да причини напукване на капака на глазура. Прекалено бавно охлаждане може да доведе до загуба на блясък глазура поради кристализация.
пожълтяване и мътност на повърхността на глазурата: В първоначалния етап на охлаждане (1410-1000 ° С) за два вида маси дефекти могат да възникнат. Пожълтяване е резултат на окисляване на желязото: 4FeO + O2 = 2Fe2O3. Железен оксид Fe2O3 придава жълт нюанс повърхност изделия. Въпреки жълт оттенък не уврежда имоти от порцелан, но се влошава външния вид на продукта. Пожълтяване може да се елиминира чрез повторно синтероване, взети заедно нормален режим. Замъгленост пудра се дължи на неговата кристализация.
С бързо охлаждане 1410-1000 ° С във въздух (окислител) среда, поради високата интензивност на началния етап на охлаждане и кристализация FeO окисляване глазура става невъзможно, при което глинен съд поддържа белота и блясък глазура.
Шеста изпичане период - охлаждане. При по-нататъшно охлаждане в температурния диапазон от 1000-700 ° С, се втвърдява течна фаза и накрая преминава от порцелан, податлив на чуплива. През този период, продуктът като термични и механични напрежения. Thermal стрес, произтичащо от температурната разлика между еластичната държавата, изчезват след изравняване на температурата над дебелината на продуктите, така че те се наричат временно. Термични напрежения могат да доведат до унищожаване на продукти при охлаждане. Когато втвърдяване на течната фаза в продукт с механично напрежение поради неравномерното свиване на масата на нейната дебелина. Тези напрежения могат също да доведат до разпадни продукти в процеса на охлаждане, и потребителя. Ето защо, механичното налягане се наричат остатъците.
Временни и остатъчните напрежения в зависимост от продукта, скорост на охлаждане през този период. Допустима скорост на охлаждане зависи от свойствата на материала, размера и формата на продукти, а също и от клетки на обхвата. За да се намали стреса на двата вида скорост на охлаждане през това време е малко намален. Освен процент намаление температура определя от термичната стабилност на продукти и пещ мебели. "