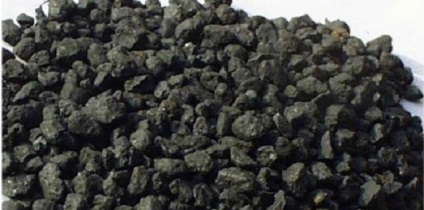
Суровини за получаване на нефтен кокс
Качеството на суровината е основната влияние върху характеристиките на крайния продукт - нефтен кокс.
производство на кокс в МИС обикновено се извършва в единица забавено коксуване (USI).
Характерна особеност на работните условия на ултразвуково изпитване е използването на смеси от различни суровини останалите по растенията, получени от нефт рафиниране.
Суровините са тежки нефтени фракции, получени от атмосферното и вакуумна дестилация, масло (мазут, polugudrony, катрани), крекинг остатъци от термичен крекинг мазут и катрани, тежки газьоли, каталитичен крекинг, остатъци от производството на масло (асфалт пропан де-асфалтирано катран, екстракти масла пречистване фенол и и др.).
От всички нефтени остатъци, податливи на различни видове структури на коксовите счита ароматни концентрати (дестилат крекинг на остатъчни вещества), както и някои други въглеводороди с високо молекулно тегло са най-предпочитани.
Поради тази причина, на суровината по-нататък дестилатни перспективни видове суровини.
Рафинерии имат различни условия на работа и работят с различни масла, така забавено коксуване единица за всяка рафинерия са били построени, за да отговарят на специфичните условия.
Сред основните параметри, определящи качеството на масло като плътност, фракционна масло и химичен състав, най-значително плътността компонент и съдържание на сяра.
Сяра - един от най-нежелателни примеси в състава на сурови масла и крайния продукт - кокс.
В зависимост от масовата фракция на серни кокс, както и масло, се класифицират като ниско съдържание на сяра, сяра, високо съдържание на сяра.
Серни кокс се различават от по-малко благоприятни свойства в сравнение с ниско съдържание на сяра кокс: корозия причина оборудване, увеличен брой на пукнатини в продукта електрод, унищожаването на огнеупорни тухлена зидария калциниране пещи, по този начин тяхното използване е ограничено до определени области.
Маслени влизащи рафинерии, се различават по състав, по-специално на съдържанието на сяра.
За България се характеризира с обработка главно сяра и високо съдържание на сяра масло.
Понастоящем основната суровина за масло кокс са сяра.
Използването на технологии за получаване на висококачествен кокс, независимо от състава на първоначалната масло, решава много проблеми:
осигурява качество електрод промишленост суровини позволява използването в производството на широка гама от масла, както и за задълбочаване на процеса на рафиниране на нефт в рафинерията.
За целите на десулфуриране на крайния продукт се прилага калциниране кокс.
Друг начин за получаване на десулфуриран нефтен кокс от кисело маслени степени - предварително отстраняване на сяра от суров нефт от хидрогениращо отстраняване на сярата, хидрокрекинг, или де-асфалтиране.
Този вариант се счита за по-ефективна, независимо от факта, че е по-сложна и изисква допълнителни разходи.
В българските растения масло се доставя предимно от магистрални тръбопроводи (МНП) Транснефт, където Уест сибирски масло, сибирски Light марка смеси с по-тежък нефт и серни Урал марката.
Методи за получаване на суров и калциниран нефтен кокс
Коксуващи масло суровина - най-твърда форма на термичен крекинг на нефт остатъци.
Това се извършва при ниско налягане и температура от 480-560 ° С, до получаване на нефтен кокс, както и въглеводородни газове, бензин и фракции на петрола керосин газове.
Когато коксуване настъпва разделяне на всички фуражни компоненти за образуване на течни дестилатни фракции и въглеводородни газове; и разграждане циклизация на въглеводороди с енергично отделяне на маслени фракции керосин газове; кондензация и поликондензация на въглеводороди и дълбок печат високомолекулни съединения, за да се образува твърд въглероден остатък.
Индустриална процес коксуване се извършва върху растения 3 вида: периодични коксуване коксови кубчета, забавено коксуване камери, непрекъснат кипящ слой коксуване носител кокс.
Бавно (полу-непрекъснато) коксуващи се е най-разпространената в световната практика.
Суровини, предварително загрята в тръбни пещи за 350-380 ° С, непрекъснато се подава в колоната за каскада тава дестилация (задейства при атмосферно налягане), преминаващ надолу, който контактува с парите нарастващите към комплекта от апарата за реакция.
В резултат на топлина и маса част от парата се кондензира, образуващ с суровина така наречената вторична суровина, която се загрява в тръбна пещ до 490-510 ° С и влиза в коксови камери - кух вертикален цилиндричен апарат с диаметър 3-7 м и височина 22-30 м.
В камерата, реакционната маса се доставя непрекъснато 24-36 часа и благодарение на топлината натрупани чрез кокс.
След запълване на коксовата камера при 70-90% от него се отстранява, обикновено с водна струя под високо налягане (15 МРа).
Cox влиза в трошачка, където е натрошен на парчета не по-големи от 150 mm и след това подава към грохот асансьор, където се разделя на фракции 150-25, 25-6 и 6-0,5 мм.
Състав, от който се изпуска кокса, остра нагрява пара и парата от работните камери на кокс и обратно напълнена коксуване маса.
Летливите коксуване, представляваща смес пара-течност непрекъснато се изтегля от камерите и действащ последователно отделя в дестилационна колона, воден сепаратор, и блок на газ към колоната газове
Типичните параметри: температура в клетките 450-480 ° С, налягане 0.2-0.6 МРа, продължителност 48 часа.
Предимства на забавено коксуване единица - висок добив на ниско съдържание на пепел кокс.
От същото количество суровини могат да бъдат получени по този метод, е 1.5-1.6 пъти повече от кокс в непрекъснат карбонизация.
В българска рафинерия управляван блок 1-блок 2 и коксов (всеки блок се състои от 2 или 3 реактори х) от няколко типа.
оформление, дизайн инсталации, направени по проекти и Giproneftezavody VNIPIneft институции.
Се провежда в хоризонтален цилиндричен диаметър апарат на 2-4 м и дължина 10-13 м.
Raw кубчета постепенно загрява от долния открития огън.
Освен това, по конвенционален начин дестилати възстановени, суши се и калциниран кокс (2-3 часа).
След това температурата в пещта се понижава постепенно при куба и на куба се охлажда първо с водна пара, а след това на въздуха.
Когато температурата на кокс се понижава до 150-200 ° С, тя се освобождава.
Типичните параметри: температура на парната фаза от 360-400 ° С, атмосферно налягане.
Методът обаче показва ниска ефективност, изисква много разход на гориво, както и значителните разходи за ръчен труд и затова се използва едва ли някога в индустрията.
Непрекъснато коксуване кипящ слой (thermocontact крекинг)
Суровини, предварително нагрята в топлообменника се свързва в реактор и се нагрява в суспензия инертен охладител и кокс на повърхността по време на 6-12 минути.
Тъй като охлаждащата течност се използва обикновено коксов прах с размер на частиците до 0.3 mm, поне по-големи гранули.
Получената кокс и охлаждащата течност се освобождава от реакционната зона и се подава в регенератора (koksonagrevatel).
Има слой охлаждащата течност се поддържа в суспендирана форма с помощта на въздух, който се изгаря в поток от 40% кокс, и голямата част от него се изпраща на потребителя.
Благодарение на топлината, генерирана от изгарянето на част от кокс, топлоносителя загрява и се връща в реактора.
За преместване на охладителните използва пневматичен коксови частици, увлечен газ или пара.
Дестилатни фракции и газове, изпускани от реактора и разделени по същия начин, както в забавено коксуване.
Типичните параметри: температура в топлообменника реактор 300-320 ° С 510-540 ° С и 600-620 ° С налягане регенератор в реактора и регенератора 0,14-0,16 и 0,12-0,16 МРа съответно охладител - (6.5-8.0)
Коксуващи в кипящ слой се използва за увеличаване на добива на светло масло. Освен това, комбинацията от непрекъснат коксуване с газификация на кокс произведени могат да бъдат използвани за производството на дизелово гориво и котел гориво.
Преди да се използва нефтен кокс обикновено се подлага на разкрасяване включва няколко процеси.
Калцинирането премахва летливи вещества и частично хетероатома (например, сяра и ванадий), намалено електрическо съпротивление.
Когато grafitirovanii 2D кристали се превръщат в кристална формация на 3-измерна ред.
Като цяло, етапа на рафиниране може да бъде представено чрез следната схема: кристалити → карбонизация (калциниране при 500-1000 ° С) на → двумерен подреждане на структура (1000-1400 ° С) → predkristallizatsiya (трансформация кристалити при 1400 ° С и по-горе) → кристализация, или графитизиран (2200-2800 ° С).
- алуминиевата промишленост, като редуциращо средство (на анодна тегло) от алуминий топене на алуминий руда (боксит). Специфичен разход на кокс от 550-600 кг / тон алуминий.
- суровина за производство на електроди, използвани в стоманени пещи;
- суровина за получаване на карбиди (калций, силиций), използвани в получаването на ацетилен;
- производство шлифоване, абразивни материали,
- в производството на проводници и други огнеупорни материали.
- като редуктори и сулфидизация средства (sernisty1 и кисели),
- за производството на химически апарат, работещ при агресивни среди в ракета инженерство и т.н. (структурен материал).
Свързани статии