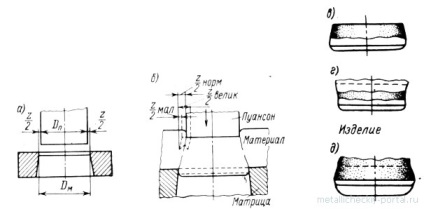
Фиг. 9. разликата между матрицата и щанцата (а), съвпадение и несъответствие
срязване пукнатини (б) и формата на частите на повърхността нарязани отсечени
при нормална (в), малък (с) и големи (б) празнините
Съгласно технологичната празнина разбере положително или отрицателно разликата между матрицата и удар работа размер G (фиг. 9а).
Разликата има силно влияние върху величината на необходимата сила на рязане и работата, качеството на повърхността на срязване, точността на частта за устойчивост на износване и умират. В повечето случаи, най-голямата стойност на практика е качеството на продукта. За да продължи части на режещо или пробиване отвори често налагат високи изисквания. Те се свеждат до факта, че разрязаната повърхност е чиста, без пропуски и пукнатини и чеп. Подробности, колкото е възможно трябва да е плоска.
Изключително важно е в качеството на въпрос рязане (пробиване) предоставя стойност на изчистване. При нормална dreschiny процеп, простиращ се от режещите ръбове на поансона и умират да съвпадне (фиг. 9 б), което благоприятства образуването на високо качество без недостатъци, пукнатини и неравности на повърхността на рязане. Такава повърхност е показано на фиг. 9 инча Горната част на детайла е с размери, съответстващи на размера на поансона и долната - матрицата. Както се вижда от фиг. 9, в част от елементите, пред които са изправени матрицата, характеристична ивица лъскав, с лек закръгляване на ъгъла; страна обърната към перфоратора е леко заострен и груб. Страничната повърхност на част (отрязана повърхност) могат да бъдат получени, като по този начин не са строго вертикални, но на външен вид доста задоволително.
Трябва да се отбележи, че задоволителни форма на отрязаната повърхност се получава, когато остри режещи ръбове на матрицата дори ако достатъчно големи хлабини -до 30% от дебелината.
В малка междина (фиг. Деветграма) срязване пукнатини не съвпадат, и други подобни са паралелно разположени една от друга. В крайна разликата между металните пукнатини и наслояване образува недостатък на повърхността на рязане. В резултат на горната част на част е оформена с втори блестящ колан опъната брус, неправилни назъбени ръбове и леко конична разширява нагоре.
В случая на голяма разлика (фиг. 9 и т.н.), с много тънък материал (1.5 mm) метал прибиране среща в междината между матрицата и щанцата с последващо счупване. Продуктът в този случай идва с дрипави разменяйте, имащи вид на затегнати ръбове. Много големи празнини (повече от 30-40% от дебелината) за рязане на дебели материали водят до образуването на силно заоблен ръб детайл от матрицата и от ръба откриване на поансона.
Качеството на повърхността на срязване засяга замъгляване на режещите ръбове на поансона и матрицата, както и неравномерното разпределение на разликата по рязане на контур. В последния случай, веригата често може да получи задоволително, а другият - с брус. Освен това, неравномерно междина води до притъпяване на част на режещата ръбове.
Неправилно клирънс и притъпи режещите ръбове на матрицата увеличава необходимостта от усилия и сеч на изпълнението.
Настройка на луфта между матрицата и удар
Размерът на разликата зависи от механичните свойства и дебелината на материала и режима на работа натиснете - броят на двойни плъзгащи се ударите в минута.
В зависимост от вида на материала и дебелината на стойността на клирънс (0.5 до 12.10 mm за дебелината) варира между 4-16% от дебелината на материала. При избора на празнина се стреми да установи своята оптимална стойност, при която да отговаря на основните условия за намаляване на четири високо качество, а именно най-малката сила на рязане, висококачествено повърхността на разреза на продукта, максимална точност щамповане и, като следствие, най-високата устойчивост печат.
При използване на по-дебел материал гама оптимално клирънс по-голяма от тънък. Това се дължи на по-малко влияние на притъпяване на режещите ръбове на инструмента, тъй като работи на образуването на мустаци при рязане дебели материали. В относително остри режещи ръбове на матрицата тънък материал позволява работа при определени интервали от разликата. По този начин, с високо качество на рязане може да бъде направено в определен интервал на пропуски за двете дебели и тънки метали. Поради това е препоръчително да се инсталира на следните идеи:
1) минималната стойност на оптималната междината (за всеки материал и дебелина) zmln. където изрязания ръб на крайния елемент става почти перпендикулярна на равнината на детайла без забележимо образуване на мустаци;
2) максималната стойност на оптимално Zmax на празнина. при което повърхността на рязане е задоволителна, въпреки че не е вертикална.
Тъй като най-малко работа (износване) умират празнина между матрицата и удар се увеличава, разликата трябва да бъде разположена в близост до минимум (zmln) за новопроизведени печат. Свободни зони, определени в зависимост от вида и дебелината на материала. С увеличаване на твърдостта и дебелина на материала от стойността на разликата като процент от дебелината на материала се увеличава.
Разликата може да бъде определена от отношението
където m - AC коефициент, като се отчита дебелината и вида на материала.
Таблица. 6 показва стойностите на минималния и максималния първоначален двустранно диаметрален за различни материали по време на работа преси броят на ударите в минута 120-140. За ножици, както и за едностранно рязане процепа на дюзата трябва да се приема като част от 2 минути.
Оптималната стойност на пропуски Zmin при рязане с повишен брой на двойно инсулти преса (п 140 / мин) трябва да се увеличи в сравнение с таблични данни в 1,5-2,0 пъти. Например, за въглеродна стомана с дебелина 2 mm оптимално клирънс е 15-20% от дебелината на материала.
Увеличаването Zmin осигурява нормален процес на рязане при по-високи скорости, тъй като в противен случай ще има "заглушаване" удар в матрица, която се получава в резултат на факта, че поансонът и умират, затопля се до неравномерно увеличаване на техните размери.
Създаването на пропастта
Беше отбелязано по-горе, че количеството събрани части зависи от размера на матрицата и размера на щанцовани отвори - от размера на поансона. Това дава възможност да се изведе правило, което определя посоката на пропастта, в зависимост от предметите какъв размер трябва да стои - външен или вътрешен. В случай на намаляване на външния контур на номиналните размери част Dout предава матрица Dm = Dn. и Z клирънс за сметка на намаляване на размера на поансона Dout. .. Т.е. Dp Dout = - Z. Когато пробиване номинални размери са дадени DH удар DP. и Z реакция се извършва чрез увеличаване матрица размер дм. .. Т.е. дм - DH + Z.
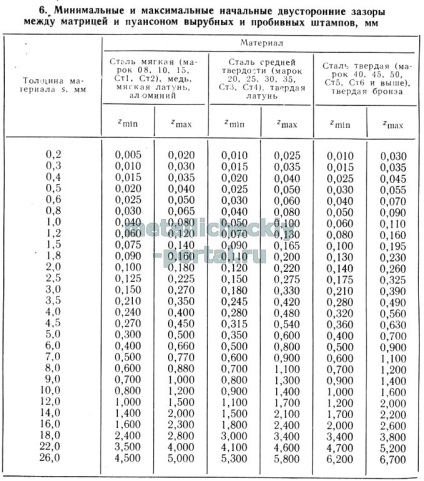