СУРОВИНИ доменни пещи
Запасите от въглища, които са много големи, може да бъде за съжаление директно използвани като гориво в доменни пещи. Въглища съдържа 20-40% летливи вещества, което е вече на нагряване до 250-350 ° С и по-горе започват да се интензивно разпределени, разкъсване на парчета на въглища за образуване на дълготрайна въглищен прах. Този прах запушва кухините между по-големите парчета от руда, агломериране, пелети, пропускливост на газ влошава колоната в такса за пещ, пещ лакирани clutters въглищен прах и отломки. Работата на доменните пещи в ъгъла винаги е свързан първо с намаляването на техническите и икономическите параметри на топене, а след това с тежки нарушения на двутактови и аварии.
Само на няколко слоя от стари въглища - каменните въглища, използван в доменни пещи с ниска надморска височина, но сегашната доставката на въглища е напълно изчерпано (Шахти антрацит в във въглищните пластове на Донбас "Мощен" в Prokopyevsk "Volkovsky" в Кемерово, Кузбас и Пенсилвания в САЩ, Великобритания и Уелс) и топене в антрацит е само исторически интерес. От това следва, че наличието на въглища в висока пещ е невалиден и трябва да се изключи напълно. Ако по някаква причина магазина организационната доменна пещ е изчерпала всички запаси от кокс в непосредствена близост до складове и цели, има много добра буца въглища, е препоръчително обаче да се спре напълно доменни пещи, кокс в очакване на пристигането. В крайна сметка на загубата на продукция в този случай ще бъде много по-ниска, отколкото, когато влизат в пещите на заплащане на въглища без да спира.
От началото на желязната епоха syrodutnyh основно гориво в пещи и след това domnitsah и доменни пещи е въглен - пиролиза продукт (овъгляване без въздух) дървен материал при 350-650 ° С С-старите е така наречения метод "препълнена" за производство на дървени въглища. Висока купчина попълнено дърво стъкло шлифовано obkladyvali трева намаза глина, оставяйки на дъното на купчината са само няколко дупки, през които купчина център получиха малко количество въздух, необходимо за изгаряне на дървесни материали. На върха на купчината наляво изходните отвори на продуктите от горенето от дърво и дървени пиролиза газообразни продукти. В съвременните пещи колички Въгленът от дървесни клинове последователно преминава през секцията пещ камера, където пиролизата на дървесина се подава непрекъснато и когато нагретите продуктите от изгарянето в пещи дърво и въглища. Такива пещи могат да схванат напълно ценните газообразни продукти pereuglivaniya дърва за огрев. Добивът на въглен от дърво варира обикновено между 60 до 74%, неговата видима плътност е 0,38 гр / cm 3 (бреза въглен) (об.); 0.29 грама / cm 3 (бор въглен); 0.26 гр / cm 3 (смърч въглища). Обемното тегло на 1 m 3 сух въглен пещ е 130-200 кг / м 3. механична якост е малък въглен и позволява да се стопи само в доменните пещи с полезна височина от 18 m.
Въглен има висока запалимост и реактивност поради огромния си порьозност (80-87%.). В тази връзка, въглена изгаря преди дюзи въздух доменни пещи в окислителната зона на малък обем, което пречи на силно нагрята взрива, също намалява размера на окислителни зони.
В момента въглен топене на чугун в голям мащаб се извършва само в Бразилия, където огромни области от района на река Амазонка се изсичат гори и период евкалипт въртене е само на 7 години (оборот изсичане на иглолистни дървета в Урал, 60-70 години). През 1982 г. в Бразилия в 134 малки доменни пещи се разтопява върху въглен 4.4 Mill. Т на чугун.
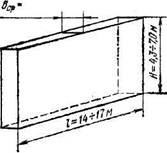
Фиг. 4. Камерата на коксовите пещи
Поради ограничения на влизащите в него XVI-XVIII век, те отново бяха многобройни опити доменна пещ за изгаряне на въглища, но всичко завърши с неуспех. Необходимо е да се създаде нов изкуствен гориво за доменните пещи. Затова гориво и става въглища кокс.
Процесът на висока температура коксуване A. Derby е изобретен през 1735, той е въглища пиролиза без достъп на въздух при 900-1100 ° С в продължение на 14-18 часа.
Помислете процес коксуващи се по-подробно.
Преди да заредите в пещ таксата въглища в кокс се смила на по-малко <3 мм. Компоненты шахты усредняются по составу на специальных складах, затем тщательно смешиваются.
След полагането на таксата в пещта и изравняване на повърхността на пещта на партидата се планира внимателно запечатани. Нагряването на заряд в пещта се появява само топлинна проводимост от две стени, в който така наречените отоплителни стени изгарят смес от доменна пещ газ и кокс и постигнати температура до 1350-1400 ° С Еволюира газове и партидата незабавно освободени от пещта през специални отвори. Както бе споменато по-горе, основната причина за унищожаване на парчетата въглища в доменната пещ е интензивно отделяне на големи количества въглища летливи вещества. Затова задачата на процеса на коксуване е да се премахне по-летливите на основната маса на коксовата пещ и създаването на фирма частици продукт, съдържащ не повече от 1.5-2% на летливи вещества, което предотвратява разрушаването на кокс в доменната пещ.
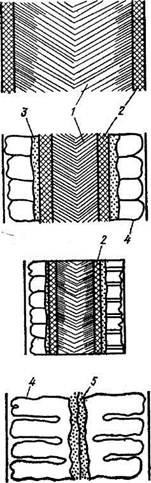
Фиг. 5. Етап коксуващи 1 - смес; 2 - пластмасовия слой; 3 - знак; 4 - кокс; 5 - аксиален вертикална пукнатина
Има следната стъпка последователно появяващи високо коксуващи се въглища:
1. сушене въглища чрез нагряване при температура до 100 -120 ° С.
2. нагряване на въглищата до 300-350 ° С Добър коксуващи се въглища в този етап преминава само частици без нагряване физическо разрушаване (разграждане) на разтопими съединения - битуми, разпадането и които са разпределени летливи вещества. По този начин, високо качество коксуващи се въглища Kuznetskii а когато се нагрява до 300 ° С освобождава само 12-15% от летливата маса. Битуми този въглерод не са унищожени, докато топене. Обратно, не-коксуващи се въглища в този етап разпределя голяма маса на летливите вещества, битуми те се подлагат на разграждане, въглища губи способността си да се стопи; не може да се получи от кокс като въглища.
3. омекване и въглища се топи при 350-500 ° С Първите стопени стопяеми битум. Полученият първичен стопилката се разтваря масата на заряда на въглища почивка. Само малка част от частиците на въглищата запазва своята индивидуалност и не се разтваря в течна фаза. летливи интензивно отличава от стопилката, което значително променя неговия химичен състав, увеличава вискозитета. Порите на кокса - това мехурчета и тръби, при което летливите вещества се премества в масата на стопилка; стена ги втвърди и след това се съхранява в крайния продукт,
4. При 500-600 ° С стопилката се затвърди в формата на първо място, все още слаб в механична връзка с продукта - Чар с провеждане обикновено около 50% (по тегло) на емисиите на летливи оригиналния такса въглища.
5. 600-1100 ° С се извършва много часове на калциниране кокс, което позволява почти напълно отстранява летливи вещества за провеждане на частичен графитизиране на кокс, т.е.. Е. Превръщането на аморфен въглерод в кристално шестоъгълна графит. Степента на графитизация на крайния коксът се оценява от експериментални данни, е 15-20%. Именно през прекристализация и синтероване агент кокс при 600-1100 ° С се увеличава здравина и твърдост от 30 до 40 пъти.
Фиг. 4 показва формата на работното пространство на коксовата пещ, която е правоъгълен паралелепипед, леко разширяване към кокса. процес коксуващи се в него две надлъжни стени на пещта в посока към оста на пещта (фиг. 5). Тъй като обемът на крайния кокс тортата обикновено е малко по-малка от тази на таксата за въглища, се формира на пай-ос вертикална пукнатина - "колапс". Така дължина кокс част обикновено е около половината от ширината на камерата на коксовата пещ.
Особено ефективен подгряване на заряда на въглища в реактор нагрява азот кипяща вана до 180 до 220 ° С Както се вижда от фиг. 6, коксуването на студената влага температура заряд въглища в аксиална зона на коксовата пещ (200 мм от стената на пещта) и след 11 часа след началото на коксуване на само 500 ° С Тя достига 1000 ° С само след 14 часа.
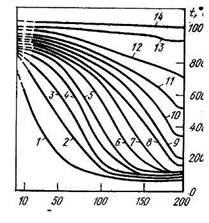
Блис на стената; mm
Фиг. 6. разпределението на температурата в коксова пещ по неговата ширина. Общата ширина на пещ камера 407 мм. Температурата в отоплителните кейовете 1300 ° С Числата върху кривите - време (часове) от началото на коксуването
2 часа). Силата на формован кокс, получен чрез технологията счита, е по-висока от силата на конвенционален кокс. първият взрив топене Формовано металургичен кокс, проведено в СССР през 1972 г. даде положителен резултат. Напредъкът в доменната пещ и техническите и икономическите показатели на топене в новото гориво да е по-добре, отколкото в Донецк кокс. Многобройни опит в чужбина са показали също, че формира кокса е пълен заместител на конвенционалната кокс.
Свързани статии