Основните геометрични параметри на съоръжения, които позволяват избор на топлинна обработка са модула (съотношението на диаметъра на делителната окръжност на броя на зъбите), външните и вътрешните диаметри на предавките, височината на зъба и дължина.
Условия за работа предавки определят тяхната специфична скорост, нивото на контакт и огъващи напрежения.
По време на работа на зъбите на зъбните са изложени на:
а) един завой при максимално натоварване (при спиране, заглушаване, по молба на максималния въртящ момент);
б) огъване на множествена циклично натоварване, в резултат на зъбния корен развиват максималните напрежения и може да настъпи повреда умора. огъване стрес може да бъде доста голям. така в някои предавки кутии ЗИЛ трансмисии те надхвърлят 600 MPa;
в) контакт напрежение на страна работа повърхности на зъбите, което води до образуването на контакт-умора питинг (точкова корозия). Ниво определя на контактните напрежения в избора на дизайн на размера на предавките.
г) износване на страничните повърхности (поради проникване на абразивни частици, мръсотия, прах в процепа) или крайните повърхности на зъбите (при превключване съоръжения в скоростни кутии). С относително плъзгане в случай на недостатъчна смазване или не смазване на работните повърхности на зъбите може да се случи "настройка" и формирането на груб на триенето, което води до много бързо износване на зъбните колела.
1. Пиньони, закаляване чрез бързо охлаждане и темпериране насипно
Зъбчати колела, работещи при ниски скорости и ниски специфични натиск (смяна на предавките) е направена от стомана класове 45, 50, 40Х, 45G2, 50G2 и подложени подобрение да се получи твърдост 220-280 HB.
За предавки, работещи при високи скорости и усилия, но в отсъствието на динамични натоварвания, 40KhN използвани марки стомана, 35HMA, 38HGN и др. В резултат на закаляване и отвръщане ниво твърдост обикновено е 43-52 HRC. Параметри режими обемен топлинна обработка се избира в зависимост от класа на стоманата. Чрез втвърдяване се извършва на универсално топлинни инсталации (камерни, шахтови пещи), което е важно предимство в малка производствена партида.
2. Зъбчати от легирани стомани нисковъглеродни, втвърдяващ химико-термична обработка
Методите на химичен и топлинна обработка втвърдени преобладаващ размер на тежко натоварени зъбни колела с модул на 3-10 mm, използвани в скоростни кутии и предаване на автомобили, трактори. Тази топлинна обработка позволява високо огъване граници издръжливост (до 1000 МРа) и контактни товар (до 2300 МРа) и висока устойчивост на износване чрез използване на евтини нисколегирани стомани. Както XTO зъбни колела за обработка използва цементацията, карбонитриране и методи нискотемпературни азотиране.
Изисквания за закалени зъбни колела цементация и карбонитриране:
а) ефективно дебелината на закалени (циментиран или nitrotsementovannogo) ef слой в зависимост от модула М трябва да съответства на следните стойности:
да се превърне в предпоставка за зъбни колела, закалени от цементацията и карбонитриране:
а) достатъчно висока закаляване и закаляване, твърдост на повърхностния слой и основните зъби по време на охлаждане в масло;
б) обработване на насищане определя ниска склонност към прекомерна свръхнасищане с азот, и повърхността на въглерод и вътрешен окисляване;
в) добра обработваемост;
г) Workability за топлинна обработка след насищане.
В зависимост от приложението и размера на съоръжения за производство на най-често използваните са:
1. Стоманени класове 15X, 20X, 18HG, 15HF, 20HF поради ниската им закаляване използват за малки умерено натоварени зъбни колела, работещи на износване (захранващи блокове предавки на автомобила).
3. Стомана 14HGN, 19HGN, 20HGNM, 20HN2M използва за зъбни предавки и основните предавките задната ос на автомобила. Те се характеризират с: висока якост, задоволително обработваемост. Молибденова стомана по-малко податливи на растеж зърно и нрав крехкост.
4. професионални легирана стомана класове хром-никелови 12HN3A, 20HN3A, 12Kh2N4A, 20H2N4A, 18H2N4MA използва за най-силно натоварени зъбни колела отговорен дестинация (масови), които са изисквания за висока якост и твърдост на повърхността комбинира с ядро висок вискозитет.
Izotverdosti проектиран диаграма диаграма закаляване и микроструктура и циментира nitrotsementovannogo слой. Ефективно използване на възможно диаграми закаляване при извършване цементацията и карбонитриране в газова среда с автоматичен контрол на потенциала насищане от въглеродна стомана (за цементацията) или въглерод и азот (ако карбонитриране). Пример диаграма закаляване за стомана 25HGT е показано на фигура 2.7.
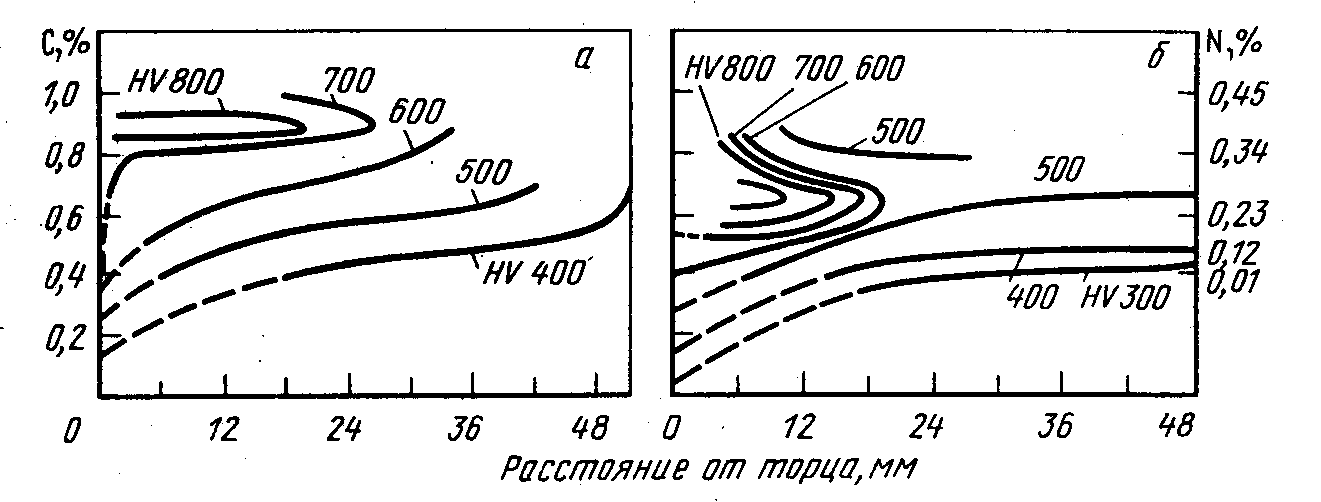
Фигура 2.7 Фигура закаляване циментира (а) и nitrotsementovannogo (б) слой от стомана 25HGT.
Използване на диаграми закаляване възможно при извършване цементацията и карбонитриране в газова среда с автоматичен контрол на потенциала насищане от въглеродна стомана (за цементацията) или въглерод и азот (ако карбонитриране).
Технология цементацията и азотиране на предавки
Циментация обикновено се използва за тежкотоварни съоръжения, в които ефективната дебелина на втвърдения слой трябва да са повече от 1 мм.
За зъбни колела с малък и среден модул с ефективно дебелина до 1 mm се използва карбонитриране. Предимства карбонитриране сравнение с цементацията газ: ниска температура на насищане (830-860 0 ° С вместо 900-930 0 ° С под циментация), по същество в същото време за обработка, подобряване на устойчивостта на износване, устойчивост на топлина и корозия. Получаване на еквивалентна якост при малки дебелини на слоя, намаляване на критичната скорост на охлаждане по време на охлаждане (поради насищане на съединението от стомана въглерод и азот), по-малките зъбни колела деформация (по-ниска температура, възможност за незабавно охлаждане, охлаждане е по-малко от необходимото интензитет).
В зависимост от клас междинен обработка необходимо и съществуващата топлинна оборудване за масово производство на уреди използват различни термична обработка верига след насищане:
а) За съоръжения на стомани 19HGN, 20HGT, 25HNTTS, 20HGNTR подлага на карбонитриране, закаляване се използва директно в студа с охлаждане (30-75 0 ° С) или гореща (160-190 0 ° С) масло.
б) За навъглеродени предавки на наследствен дребнозърнести стомани 18HGT, 25HGT, 20HNM, 25HNTTS, 25HGNMAYU използва директно охлаждане с podstuzhivaniem части температура цементацията до 830-860 0 ° С охлаждане се осъществява чрез охлаждане в студена или гореща масло.
Ако е необходимо, междинните (след циментация) машинни части след цементация забавено охлажда до специално звено камера до 250-300 0 ° С Крайното втвърдяване се извършва чрез нагряване в пещи или агрегати със защитна атмосфера или чрез индукционно нагряване.
в) За съоръжения от високи хром-никелови стомани директно охлаждане не се прилагат поради икономия в структурата където голямо количество остатъчен аустенит, и намаляване на твърдостта на HRC 45-55.
Такова съоръжение след пещта цементация се охлажда до 0 ° С 300-450 (или къща), и след това изпълнява високо отвръщане при 600-650 0 ° С, последвано от бавно охлаждане. За втвърдяване съоръжения загрява отново до 790-820 0 ° С в защитна атмосфера и се охлажда в масло.
Можете да прилага намалена цикъл топлинна обработка (без висока температура закаляване):
Вариант 1: бавно охлаждане след цементация и след втвърдяване при ниска температура на нагряване (770-790 0 ° С), охлажда се в гореща среда (140-150 0 ° С) в продължение на 3 часа;
Вариант 2: podstuzhivanie в пещта от температурата цементация до 900 0 ° С, последвано от охлаждане на въздух или podstuzhivanie до 820 0 С, последвано от охлаждане в масло. След това се прилага за закаляване претопляне до 790-820 0 С.
Заключителни операции предавка топлинна обработка във всички случаи е ниска температура темпериране най 160-200 0 ° С
Свързани статии