В дванадесетата статията цикъл "Основи и технологии граница сканиране дизайн може да се провери" предоставя общ преглед на хардуера на системата onTAP фирмата Флин Systems, предназначени за чифтосване с JTAG-PP и възли от тестовете.
Планираният ниво на качество и надеждност на продуктите се определя от големината и очакваната максимална стойност на ремонтните работи, които ще се проведат в гаранционния срок, в зависимост от изискванията на клиента, условията на работа на продуктите и на правилното им стратегия.
Ако потребителят в договора за доставка на 10 хил. Инструменти изисква гаранционен срок е 10 години, с географията на ползване се прилага за цялата територия на Русия, и на ремонта се очаква да се извърши на производителя сам, че е лесно да се изчисли, че с провала на 1% Вие ще трябва да направи 100 пътувания за гаранционни ремонти.
Разходите за гаранционни ремонти са планирани, обикновено на ниво 2-4% от продажната цена. Ако инструментът е на стойност 100 хиляди. Разтрийте. извършване на ремонти на всички страни, в размер на 3 милиона. рубли могат да бъдат планирани. Това означава, че средно едно пътуване могат да бъдат изразходвани до 30 хиляди души. Разтрийте. Ако по-горе оборудване ще бъдат експлоатирани предимно в западната част на Сибир и Далечния изток, предвидените средства няма да бъдат достатъчни. Ако устройствата са 10 хиляди. Разтрийте. и в страната - 100 хиляди парчета .. Ситуацията се усложнява и от рязко, тъй като прогнозните разходи за гаранционни ремонти ще се увеличи десетократно, и могат да надхвърлят планираното ниво на печалба. Увеличаването на продажните цени, за да компенсират тези разходи ще намалят конкурентоспособността на своите продукти и могат да бъдат пречка за изгодни договори. С оглед на изложеното по-горе става ясно, най-често срещащи стойност на планираното ниво на погрешност: 0.1% или 1000 ррт.
Използвайки данни от горните примери, опитайте се да се изчисли максималните разходи за ремонт в производствения процес. Ако структурата на единичната цена (100 хиляди. Разтрийте.) Gain е 20%, цената е равна на 80 хиляди души. Разтрийте. В структурата на разходите на компонентите, аксесоари и материали съдържат 70% (типична стойност в производството на електронни устройства) и работи - 30% (24 ти ..). Приема се, че устройството има една платка компоненти дизайн 1000 и 3000 спойки. При използване на първокласен монтаж оборудване на възможно най-висок ниво на дефекти е 100 ррм в средата на голям купон. В този случай, 10 хиляди. Брой в играта. Получаваме печатни платки възли:
3, 000 · 10000 · 100/1 000 000 = 3 000 потенциално дефектни запоени връзки.
Първокласни електронни компоненти доставчици и производители гарантират скорост дефект от 10 части на милион. Това означава, че 10 хиляди. Брой в играта. получаваме:
1000 · 10000 · 10/1 000 000 = 100 потенциално дефектни компоненти, т.е. 31% запоени печатни възли съвет ще разполага с потенциалните дефекти.
своевременна диагностика и местоположението на дефекта на електронния модул има 1000 компоненти, средно не по-малко от 4 часа. При средна цена на труда пъти за висококвалифицирани специалисти $ 25. САЩ (включително режийни), разходите за ремонт при издаването на партийните устройства без означава автоматично диагностика и локализиране на дефекти ще бъде:
3 100 · 4 х 25 = 310 до $ 000 или около 10 млн.
Средната минимална цена на ремонт на устройството ще бъде: 10 000 000/10 000 = 1 000 рубли. През втората, изчисленията са валидни, ако всички печатни секции, за да се обработват в една партида, защото в началото и в края на играта нивото на дефекти, обикновено няколко пъти по-висока (в началото на играта, която трябва да се премахне последиците от човешки грешки и неподходящо използване на компоненти и аксесоари, както и в края на краищата - последствията от липсата на компоненти). Освен това, дори и най-квалифициран контролера военнослужещ / трафик и най-съвестните надзорни органи не могат да си позволят да потвърдим напълно своите продукти в съответствие със своя дизайн и регулаторна документация. В резултат на това - допълнителни разходи за ремонт на устройства, които не успяват по време на тестовете за приемане и на потребителите по време на гаранционния период.
Горните примери ясно потвърждават добре познат постулат на "разходите за отстраняване на дефекта е по-ниска, по-близо до мястото на настъпване на потенциала той отбелязва:" и това означава, че е необходимо да се потърси производство на качествени и надеждни продукти в завода.
По втория въпрос: каква технология постига планираното ниво на качество и надеждност, и това, което разходи са необходими за това? Така че, ние сме дефинирали целта: да се разработи и приложи технология, която осигурява редовни (изчислен) нива на качество и надеждност на продуктите, с минимално (оптимално) цена.
Да разгледаме пример: за вх-TII вградени типичния производствен процес на печатна платка възли монтаж (виж фигура 1 ..).
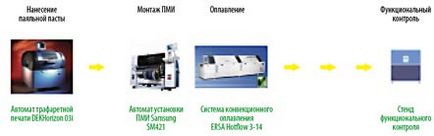
Фиг. 1. Технологичен процес на сглобяване на печатни платки възли, без системи за контрол и инспекция
След въвеждане на системата за контрол на качеството на AOI спойки монтаж и дефекти на продукти, свързани с отместване компонент води по отношение на контактните подложки на платката, значително е намалял. В съответствие с предложената алгоритъм (виж. Фиг. 2) взети конверсия за диагностика и локализиране на споменатите видове дефекти може да се счита за задоволително.
Таблица 2. Критерии за качество на компонент монтаж повърхностен монтаж в съответствие с изискванията на различни стандарти
Дефект - клас 1, 2. страничното преместване (А) надвишава 50% от ширината на контактната повърхност (W) или 50% от ширината на контактната подложка (P) (избрани минимална стойност).
Дефект - клас 3.
Страничното изместване (А) надвишава 25% от ширината на контактната повърхност (W) или 25% от ширината на контактната подложка (P) (избрани минимална стойност).
Дефект - клас 1, 2. страничното преместване (А) надвишава 50% от ширината на контактната повърхност (W) или 50% от ширината на контактната подложка (P) (избрани минимална стойност).
Дефект - клас 3.
Страничното изместване (А) надвишава 25% от ширината на контактната повърхност (W) или 25% от ширината на контактната подложка (P) (избрани минимална стойност).
стр. 10.7 (фиг. 50) Дефект "странично изместване" (А) надвишава 10% от ширината на контактната повърхност (W).
Дефект - клас 1, 2. максимално странично преместване (А) надвишава 50% от широчината на изхода (W) или 0.5 мм (по-малката стойност се избира).
Дефект - клас 1, 2. максимално странично преместване (А) надвишава 50% от широчината на изхода (W) или 0.5 мм (по-малката стойност се избира).
Дефект "максимално странично изместване" (А) надвишава 25% от широчината на изхода (W).
Дефект - клас 3. максимално странично преместване (А) надвишава 25% от широчината на изхода (W) или 0.5 мм (по-малката стойност се избира).
Дефект - клас 3. максимално странично преместване (А) надвишава 25% от широчината на изхода (W) или 0.5 мм (по-малката стойност се избира).
Следващата най-голямата тип дефект е "избран неподходящ компонент" (ред 3 в таблица 2 и фигура 2). Най-вероятните причини за неправомерни крепежни елементи могат да бъдат:
- грешка на оператора с захранващото съоръжение;
- дефектен компонент (брак производителя);
- повреда на компонент в производствения процес (процес дефект) на.
Най-ефективните средства за диагностика и локализиране на дефекти от този тип е автоматичен контрол в съединение. Предвид монтирането на висока плътност на продукти и тяхната широка гама от в SPEA4060 система (вж. Фиг. 4) е избран като средство за автоматичен електрически контрол в съединение.
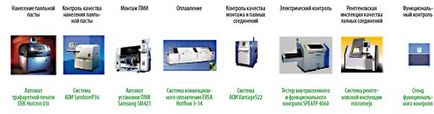
Фиг. 4. Процес Диаграма на потока монтаж на печатни платки събрания в прилагането на съвременна автоматизирана система за инспекция и контрол
След въвеждането на автоматична SPEA 4060 контрол по веригата на броя на дефекти на продукти, свързани с инсталирането на грешен елемент е значително намален. В съответствие с предложената алгоритъм (виж. Фиг. 2) за превръщане на полученото диагностика и локализиране на дефекти от гореспоменатия тип може да се счита за задоволително.
Следващата най-важният вид на дефект - "недостатъчно количество спойка в спойки" (линия 4 в Таблица 1 и Фигура 3.). Най-вероятните причини за незадоволителното размер на припой могат да бъдат:
- неправилен размер на подложки (конструктивен Тора грешки);
- неправилен размер на отвора (грешката дизайнер);
- лошо качество на шаблон (шаблон производител дефект);
- лошо качество спояваща паста (дефект оператор и / или производителя);
- ниско качество на спояваща паста за работа (процес дефект);
- неправилни настройки на екрана на принтера (скорост на преместване и / или налягането на острието на лекар);
- увиване на печатната платка.
Грешки дизайнери трябва да бъдат идентифицирани при етапите на приемане на конструктивна документация, технологична подготовка на производството и производството на прототипи - преди постановка продукти в масово производство. Качеството на шаблони, спояващи пасти и печатни платки трябва да се контролира от един входящ контрол.
Качество на спояваща паста за различни приложения, управлявани от съответните стандарти (вж. Таблица. 3).
Таблица 3. Критерии за приемане на качеството спояваща паста според НАСА-STD-8739
Пастата трябва да се прилага в точен регистър с контактните подложки, както и да има еднаква дебелина. Без мостове, мехурчета, кора и смазване.
НАСА-STD-8739.2 [8,2], [8,6]
мостове Образование - показател за неверни параметри на процеса спойка паста.
НАСА-STD-8739.2 [8.7.4.f], [12.6.1.a.1]