Методи за формиране на винтови повърхности на частите могат да бъдат класифицирани по вид на обработващи инструменти. Фигура 2.1 показва методи за класификация за производство на спирално повърхности на частите. метод за подбор за производство на компоненти с винтова повърхност зависи от материала (метал, пластмаса, стъкло и т.н.), за изискванията към работните условия.
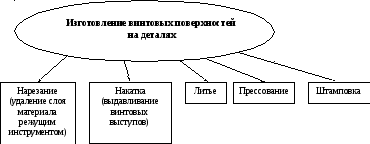
Фиг. 2.1 методи за класифициране на производството на спирално повърхности на части
Широкото метод за производство на резбованите части на производствени процеси се резби. С резба резачки и гребени на стругове резба се извършва за външен и вътрешен (вътрешна резба като се излиза от D = 12 mm и по-висока). Този метод се характеризира със сравнително ниска производителност, така че сега тя се използва главно в малък мащаб и индивидуално производство, както и в създаването на точни винтови уреди, вретена и т.н. Предимството на това - простотата на режещия инструмент и относително високата точност на конеца.
Процес резби нож извършват в няколко пропуски, броят на които зависи от терена и височината на профила на резбата и други фактори.
Схематично метода за вдяване на инструмента, показан на Фигури 1.1 - 1.4, 1.7, т.е. Това е, както следва: а части въртеливо движение, на които се нарязват на конеца и движение на режещото транслационно (по оста на частта), последният отстранява (премахва) част повърхност под формата на винтова линия.
При рязане на движение резба, по-специално с голям профил, често се използват два режещото резба за получаване на нормален профил.
Процес резби mnogozubyh гребен срещу нарязване нож е по-продуктивни. Гребен, работна част от които се състои от 5-8 зъба, е от порядъка на различна височина на зъбите, последният от които са калибрирани и да имат пълен профил.
чрез намаляване на работа се разпределя между няколко гребен зъби, като по този начин намаляване на броя на преминавания и намалява времето за обработка (фиг. 2.2).
Фиг. 2.2 Тема гонене
Рязане на монтажния конец в производството на партида и маса прави на стругове, купол и специални машини, с помощта на заровете, умират глави и кранове.
Най-често срещаните инструменти резби:
плаки - за резби пръти (болт, винт, щифт и т.н.), т.е. външна резба (фиг. 2.3). Според техните характеристики на дизайна плочи са разделени на кръг (преследвач) и плъзгащи (kluppovye).
кранове - за разливане на гайката в резбови отвори (фигура 2.4.).
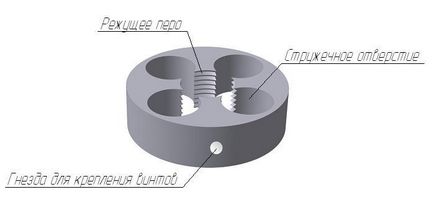
Фиг. 2.3 Plate кръг (преследвач)
Кранът е стоманен прът с резба нарязани върху него и разделен от праволинейни надлъжни или винтови нарези, които режещи ръбове. Тези канали служат за освобождаване чип. Според начина на прилагане на крановете са разделени на ръчно и машинно. Резба набор от две или три докосвания (малки, средни и нормално довършителните) в зависимост от размера му. За метрични Твърда смола и инчов резба комплект се състои от три разклонения, за метричен фино смола и тръба резба - от двете.
Тъй като устройството на инструмента резба (например: умре чешмяна) или когато прибиране на ножа, преходът от част повърхност с пълния профил резба (парцел л) до гладката повърхност е оформена дължина участък (L1) с постепенно намаляваща височина на профила (фигура 2.5). ,
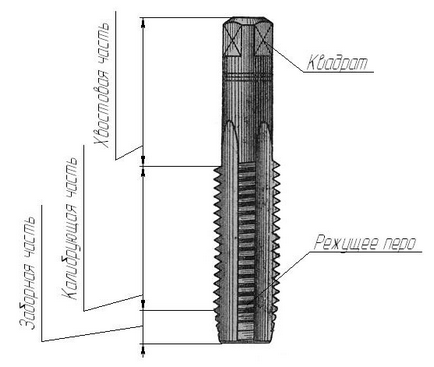
Този сайт (L1) с непълна резба наречен резба биене. Такова sbeg формира края на сляп отвор с резба кран в приложението, в което част ограда има конична форма (фиг. 2.4, 2.7). Ако конецът се извършва върху повърхност, не позволява на инструмента да го накара да спре, конецът се формира undershoots. Биене и undershoots форма Nedorezov резба (фиг. 2.5). Ако е необходимо да се получи пълна резба на профила на прът, към изхода на инструмента за резба направи жлеб ширина б. d2 диаметър. който е по-малък от диаметър D1 на резбата (фиг. 2.6) вътрешен.
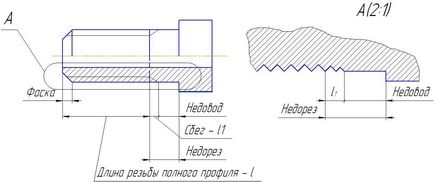
Фиг. 2.5 външна резба
За да се получи пълен профил резба в отвора направя ширина В1. d3 диаметър. който е по-голям от номиналния диаметър D на резбата (фиг. 2.8).
Обикновено за вдяване на края на буталния прът и отвора направен в крайна скосяването предпазва намотките от увреждане и е насочване на резбово съединение (фигура 2.6 -. 2.8). Размер l0 показва позицията на отвора на крайните части (фиг. 2.8).
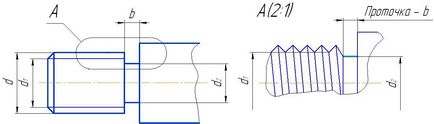
Фиг. 2.6 Използването на пълна резба на буталния прът
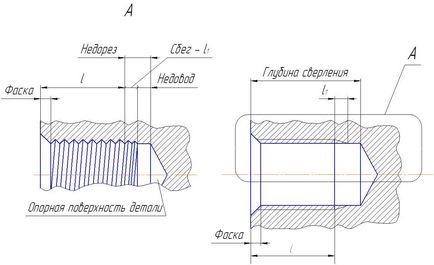
Фиг. 2.7 резба в жлеб
Размери фаски, биене и Nedorezov стандартизирани отвори (ГОСТ 10549-80 * ГОСТ 27148-86 продукта Добив закрепване резба, биене, Nedorezov и записан размери ..).
Фиг. 2.8 пълен профил резба в отвора
Последователността на производство на глух отвор в пробивната част и схематични чертежи е показано на фиг. 2.9. В началото на бормашина се пробива слот чиято дълбочина зависи от пластичност на материала, където впоследствие се завинтва парче (игла, завийте ...).
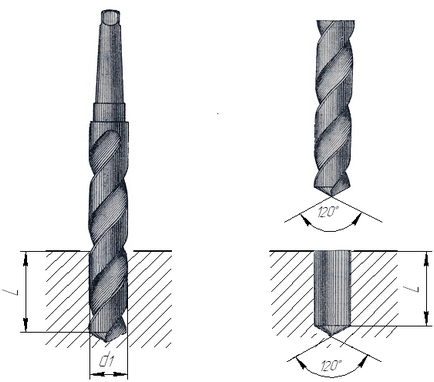
Фиг. 2.9 рязане глух отвор тренировка
Диаметърът на тренировка трябва да се избира от таблицата в зависимост от стандартите на спиране на по-нататъшното резби. d 1 дупка с диаметър е равен на диаметъра на отвора, който е пробит, L - дупка дълбочината на сеитба.
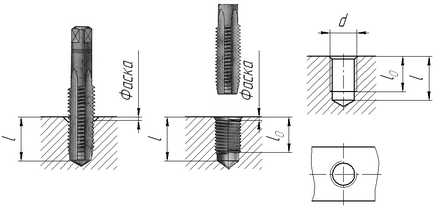
Фиг. 2.10 Използването във вдлъбнатината
Метод за производство на сляпо резбован отвор за разливане и схематично е показано на фиг. 2.10. Моля, имайте предвид, че под увити щифт или винт остава незаето част от гнездото. Тази долна част на гнездото има граница на пълна резба, нишката на непълна профил - бягство от дъното на фаска част на кран и нарязани част. Фаски по плавен отвор се извършва преди подслушване. номинална резба г диаметър, равен на диаметъра на крана, л - обща дълбочина на отворите, l0 - дължината на целия профил конец.
2.2 Опаковъчна резба
Основният промишлен метод за производство на нишката в момента е подвижен по специални конци и валци. Тези машини осигуряват изпълнение на High Fidelity форма, размер и конци чистота повърхности. процес валцована резба е да осигури резба на повърхността на детайла без отстраняване чип чрез пластична деформация на повърхността на детайла. Този процес се извършва по два начина: чрез използване на плоски или кръгли матрици (ролки). Схематично подвижен метод е, както следва. Подробности се навива между две плоски матрици (фиг. 2.11, а) или цилиндрични ролки (фиг. 2.11, б) с профил на резба. В резултат на прът е натиснат от същия профил на резба. Най-големият диаметър 25 мм се навива резба. най-малката - 1 мм. валцована резба дължина 60 - 80 mm.
Фиг. 2.11 Опаковъчна резба
2.3 Тема смилане
Фрезоване на вътрешни и външни резби, произведени по специални машини rezbofrezernyh. Въртящият резачка с радиални съкращения гребен хранене в част тялото и мелници за конци нейната повърхност. По този начин има аксиално движение на нож част или специална копирна машина със сума, равна на терена на конеца от елементите, по време на една революция.
Фиг. 2.12 показва резба смилане използвайки профил на диск за рязане. Тези ножове често намират приложение в смилане триъгълна и трапецовидна резба с голяма стъпка на части с по-голяма дължина.
Фиг. 2.12 Тема фрезоване
2.4 Шлифовъчна точност резба
Смилане Метод създаването на нишката се използва главно за да се получи точна резба в относително кратък резбовани части, като резба капачки - калибри резба ролки.
Тема смилане се извършва едновременно чрез един профил и мулти-кръг. Шлифовъчния диск е избран в зависимост от параметрите на нишката, материал на заготовката и вида на смилането (един или multistrand). Предварително в зависимост от профила на резбата профилиране шлифовъчния кръг се прави с помощта на специален инструмент, с диамант. РЕЗЮМЕ резба смилане е смилане колело, разположен по отношение на детайла при повдигане ъгъл нишка по време на бързото въртене и хранене по оста от стъпката на резбата на съкращения революция (са земята) част на повърхността на детайла. В зависимост от дизайна на нишката на машината и други фактори, се смила в две, четири или повече преминавания. Фиг. 2.13 диаграма шлайфане резби един ред на шлифовъчния диск. Тъй като стружките набразден шлифовъчни, много тънки и външната и вътрешната резба се получава много точно.
Фиг. 2.13 Шлайфане резба
Свързани статии