Съставът на разтвора на никел-покритие.
Най-широко намерено химически покритие никел, мед, сребро, паладий, кобалт и по-малко калай, хром и други метали.
Химическа никелиране. Възстановяване на никелови йони от разтвори поради окисляване на общата реакция хипофосфит
В това възстановяване може да се извърши, както следва:
Ni2 + + 2Н = Ni + 2Н +
Зараждащата водород фосфит възстановява фосфор, така че покритието на никел съдържа 6-8% от фосфор, който до голяма степен определя своите специфични свойства (Таблица 24)..
24. химически и електрохимически свойства на покритието с никел
Въпреки факта, че никел се отлага чрез химически средства, има голяма устойчивост на корозия, не може да се прилага за защита от корозия в средата на азотна и сярна киселини. След топлинна обработка никел има твърдост HV 1000-1025.
По принцип никел процес е както следва. Детайли на стомана, мед и негови сплави подготвят същите, както и за галванично покритие.
Никел покритие се извършва в разтвор със следния състав (г / л):
Никел сулфат 20
Натриев хипофосфит 25
Натриев ацетат 10
Тиокарбамид (или малеинов анхидрид) 0.003 (1.5 - 2)
Температура 93 ± 5 ° С, скоростта на нанасяне е 18 микрона / час (при 90 ° С и плътност натоварване на 1 дм 2 / л), рН = 4,1 ÷ 4,3.
Детайли в процеса на никелово покритие е необходимо да се разклаща. Могат да бъдат заменени с тиокарбамид с малеинов анхидрид в количество от 1.5 - 2 гр / л.
За започване на отлагането на никел върху части от мед и негови сплави е необходимо да се осигури тяхното контакт с стомана или алуминий. Процесът се провежда в порцеланови или стоманени контейнери облицовани с полиетилен и в контейнери от силикатно стъкло.
С отлагане висока скорост и висока плътност прост профил част натоварване препоръчва разтвор със следния състав (в г / л):
Никел сулфат 60
Натриев хипофосфит 25
Натриев ацетат 12
Борна киселина 8
Амониев хлорид 6
Температурата на разтвора 93 ± 5 ° С, скоростта на нанасяне е 18 микрона / час (при 90 ° С и плътност на натоварване 3 дм 2 / л), рН = 5,6 ÷ 5,7.
След неелектрически никелови елементи промиват в коша и след това към потока на студена и топла вода, суши се при 90 ± 10 ° С в продължение на 5 - 10 минути и се обработва термично при 210 ± 10 ° С за 2 часа (с цел отстраняване на вътрешния стрес и подобряване силата на адхезия към основата). Освен това, в зависимост от условията на експлоатация на части лак третира хидрофобна течност (NGL и др.) Или без третиране се подава към възела.
Основните причини за лошо покритие на химически никелиране на са:
1) спонтанна нанасяне на никел под формата на черни точки поради лоши почистване на бани, наличието на следи от никел или други огнища на кристализация на дъното и стените на ваната, а също и поради прегряване на разтвора;
2) наличието на непокритите обекти на елементи на сложна конфигурация, поради образуването на газови мехурчета и неравни части промивен разтвор;
3) частично нанасяне на никел върху вътрешната повърхност на банята поради докосва части на стените или дъното на ваната в процеса на никелиране;
4) намаляване на киселинността на разтвора (крак, трошлива покритие);
5) увеличаване разтвор киселинност (груб покритие и грапавост).
РН се регулира чрез добавяне на 10% разтвор на оцетна киселина или натриев хидроксид.
Детайли на силиций никел в алкален разтвор със следния състав (в г / л):
Никел хлорид 30
Натриев хипофосфит 10
Натриев цитрат 100
Амониев хлорид 50
Скоростта на отлагане на 8 цт / ч, рН = 8 ÷ 10 (поради въвеждането на NH4 OH).
Редът на химически никел покритие керамика: обезмасляване в алкален разтвор и химически повърхност ецване (смес от сярна и флуороводородна киселина), разтвор на чувствителност (150 г / л) натриев хипофосфит при 90 ° С, никелиране в алкална баня. Дебелината на частите на покритието в зависимост от техните работни условия, описани в таблицата. 25.
25. Стойностите на покритие с дебелина в зависимост от условията на работа
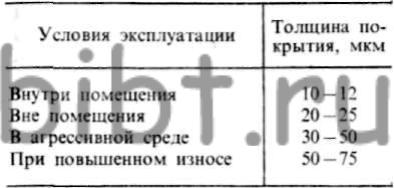
По този начин, при рН = 5,5 в утайките, съдържаща 7.5% фосфор и 3,5 при рН = 14.6%. Повишена твърдост покритие 1100-1200 кгс / mm 2 при 200-300 ° С е причинена от фаза освобождаване Ni3 Р, което кристализира в тетрагонална система с решетъчна константа = б = 8,954 • 10 -10 m и а = 4,384 • 10 -10 м. Максимална твърдост никел съответства на 750 ° с Еластичния модул в този случай е 19 000 кгс / mm 2 Якост на опън е 45 кгс / мм2 (при 20 ° С) и 55 кгс / mm2 след топлинна обработка при 200 ° С в продължение на 1 час. Коефициентът на триене покритие (с товар > 10 кг) след прилагането му същото като и блестящ хром. Специфично износване никел покритие при 100 ° С е 2 • 10 -3 mm 3 / m.
Докато се разбърква киселият разтвор се увеличава утаяване блясък и скорост на отлагане. Ако процесът на отлагане е прекъснат за няколко минути, елементите могат да бъдат заредени в банята, без допълнително активиране. Когато продължителни периоди (24 часа) на елементите да се съхранява в разтвор студен никелиране, и след това се прехвърля в работната вана.
скоростта на отлагане на метал, по-малки по-ниско рН на разтвора. В допълнение, скоростта е функция на връзка Ni2 +. Н2 PO - 2. следва да варира между 0.25 до нормална кисела баня - 0.60 (за ацетат буфериран 0.3-0.4).
В присъствието на амониеви соли се понижава скоростта на нанасяне. В наскоро получава процент разтвор отлагане първоначално високо и след това намалява с възрастта. Така, в ацетат и цитрат разтвори намалява от 25 до 25 м / час. най-оптималната скорост на отлагане
подготовка на повърхността покритие Luster се определя като база, която трябва да се полира. В алкални бани покритие, получено по-блестящ, отколкото в киселина. Покрития, съдържащи <= 2% фосфора — матовые, 5% фосфора — полублестящие и => 10% фосфор - много лъскава, но с жълтеникав оттенък. Разпръсна на дебелина 30 микрона дори сложни конфигурации на детайлите, например, не повече от 1-2 микрона. Когато баня се работи при постоянно рН, количеството на фосфора в покритието е пропорционална концентрация хипофосфит в банята.
Първият знак за нестабилност на състава на разтвора е образуването на бяла пяна поради прекомерното освобождаване на водород в целия обем на банята. След много фина черна суспензия на Ni-P, който ускорява разлагането на реакционния разтвор.
Нивото на разтвор в банята трябва да се поддържа постоянна, тъй като намаляването му чрез изпаряване води към концентрирания разтвор. Подробностите на процеса на нанасяне на покритие не трябва да се допуска от нагреватели (пара teploelektronagrev и др.).
За разлика от хидразин, натриев хипофосфит е важно предимство, тъй като утайката съдържа 8 - 10 пъти по-малко газ. Добавянето на натриев тиосулфат намалява порьозността никел. По този начин, с дебелина 20 микрона се намалява от 2 до 10 пори / см 2. При избора на материал за баня трябва да се счита, че разтворите се изпаряват при температура приблизително равна на точката на кипене, и имат висока чувствителност към различни замърсители. В допълнение, материалът трябва да бъде устойчив на HNO3. тъй като стените периодично от банята трябва да бъдат отстранени утаяване никел. Баните на 20 литра, изработени от огнеупорно стъкло и други - полирани керамика. Вътрешната повърхност на стоманените контейнери, покрити с стъкловиден емайл. Бани от устойчиви на корозия стомана трябва да се пасивирани в концентрирана азотна киселина в продължение на няколко часа. За да се избегне галванична вана между стоманата и стената му част да бъде покрита, трябва да бъдат покрити със стъкло или гума. Тъй като лайнер нисък капацитет в бани, използващи полиетиленови лайнери.
След всяко разтоварване части, електрически нагреватели, тип прът трябва да бъдат гравирани в HNO3.
Дефектен покритие на стоманените части, титан и алуминий, за да бъдат отстранени в концентрирана азотна киселина при температура не по-висока от 35 ° С, с части, изработени от устойчиви на корозия стомани в 25% разтвор HNO3. и с мед и медни - анодно разтваряне на H 2SO 4.
С цел да се подобри стабилността на състава на решение чуждестранни компании препоръчват да прибавите соли на хрома. Порьозността на покритията, получени в разтвор, съдържащ 10 г / л K3 Fe (CN) 6 и 20 г / л NaCl, определена в рамките на 10 минути. Порите са напълно отсъстват в дебелина на покритието => 100 микрона.
Пьотър Степанович Мелников. Наръчник на галванопластика в машиностроенето. 1979.
Свързани статии