1.2 катод Разпрашване
Катод разпрашване е един от най-добре известните методи за покритие. Дори през 1852 г. беше установено, че по време на преминаването на електрически ток през изредените газове настъпва разрушаване катод и депозиран покритие на стените на камерата.
верига устройства за нанасяне на покритие чрез катодно разпрашване са показани на фигура 3.
В най-простия вариант (фигура 7.18, а) Устройството се състои от разпрашващ катод 5, на който е поставен потенциал от 1 до 10 кВ, и анода разположени на повърхността на изделия 3. Между катода и анода, обикновено клапата. В началния етап на процеса произвежда евакуиране вакуумната камера в максимална степен на разреждане (
10-1 ... 10-2 Ра), и след това лепинговане се извършва в работната камера на инертен газ (аргон). Налягането в камерата е 1 ... 10 Ра.
Фигура 3 - Схематични диаграми на катодно разпрашване системи: а) диод; б) диод с отместване; в) триодно; г) с помощно йонен източник 1 - камера; 2 - държач на субстрат; 3 - парче (субстрат); 4 - мишена; 5 - катод; 6 - екран; 7 -Power блок (DC или висока честота); 8 - доставката на работа на газ; 9 - изпомпване; 10 - горещ катод; 11 - анод; 12 - йонен източник
Следващата операция е да осигури анод-катод потенциална разлика (0,5. 10 кВ). Резултатът е газоразрядни в камерата за обработка. Под влияние на йони на повърхността на катода е унищожаването на оксидни слоеве, са почти винаги присъства на повърхността. Разпръснати метални атоми реагират с реактивни газове (кислород, азот) и получените слоеве са депозирани замърсени неконтролирани примеси. В този случай, обаче, понижаване на парциалното налягане на реактивни газове в камерата, обаче, като правило, в началния етап на нанасяне на процеса на покриване се извършва на клапата. След известно време, клапанът се отваря и отива нанасяне покритие върху повърхността на продукта. Пулверизирани атома в предложението към субстрата претърпяват много сблъсъци. В резултат на разпръснати целевите атоми губят енергия, което води, като правило, намаляване на адхезия на отложения слой. За да се намалят загубите на енергия на бомбардирани атоми в хода на тяхното движение в разстоянието на газова фаза между анода и катода се направи минимална.
Процесът на разсейване може да се проведе в химически активна среда, която е специално генерирани в работната камера. В този случай процесът се нарича реактивен катодна покритие. Този метод се формира на повърхността на субстрата слоеве на окиси, нитриди, метални карбиди на.
По този начин, разпрашване се характеризира със следните предимства:
1) процеса на разпръскване на газова фаза без инерция, при прекратяване на прилагането на потенциал за производство на газова фаза катод и престава почти мигновено;
2) ниска топлинна въздействие върху изделието (само повърхността се нагрява катод);
3) възможност за пръскане огнеупорни метали;
4) възможност за получаване на покрития с различен химически състав (например, от реактивна катодна разпрашване);
5) осигуряване на висока хомогенност на отлагане;
6) остава стехиометричен състав на покритията в тяхното получаване разпрашаване от целевата сплав.
Основните недостатъци на катод разпрашване:
- ниски темпове на растеж покритие (до 1 пМ / S);
- нискоенергийни частици, степента на йонизация и, следователно, ниски адхезивни покрития;
- висока степен на покритие на замърсяване атоми газова фаза;
- присъствие в покритието на висока плътност радиационни дефекти, причината за което е влиянието върху повърхността на високо енергийни електрони, отрицателни йони.
За да се намали степента на замърсяване на покрития за повишаване на тяхната адхезия се препоръчва да се поддържа температурата на субстрата по време на процеса на отлагане достатъчно висока (400 ... 500 ° С). В някои случаи, за да се получи висококачествени покрития се използва йон бомбардиране на нарастващото филма на инертен газ, което се постига чрез прилагане на отрицателен потенциал на субстрата или чрез прилагане на допълнителен йонен източник.
При прилагането на отклонение потенциал към субстрата едновременно с отлагане на покритие процес пръскане нарастващото покритие, което обикновено не е еднаква и зависи от структурата на електрическото поле на повърхността. Поради това, при определени условия може да се наблюдава селективен пръскане и дори пълно отстраняване на покритието на определени места. Друга особеност на технологията за покритие чрез катодно разпрашване е рязък спад в скоростта на нанасяне покритие през реактивна разпрашване във формирането на мишена на химично съединение с ниска електрическа проводимост.
Тъй като скоростта на нанасяне на разпрашване на покрития е ниска, тя се използва главно за производството на тънки защитни и антифрикционни покрития върху машинни части, прецизни и устройства (газ носещи блокове, инструмент плъзгащи и търкалящи лагери). Покривният материал е молибденов дисулфид, злато, сребро, олово и индий.
1.3 магнетронно разпрашване
Магнетронно разпрашване - един вид диод за разпрашаване. Образование пара разпръсква вещество се появява в резултат на бомбардиране на целта от йони на работен газ, които са оформени в плазмата анормален отговорност блясък. Най-проста схема магнетронно разпрашване е показано на Фигура 4.
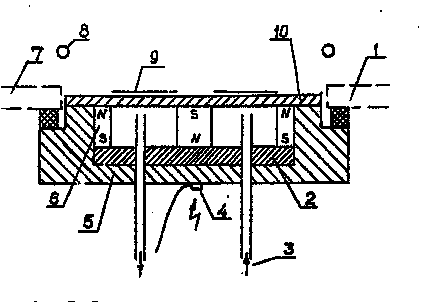
Фигура 4 - схема пленарна магнетронно система: I - уплътнението; 2 - база; 3 - канал за вода; 4, 5 - дело 6 - постоянни магнити; 7 - вакуумна камера; 8 - анод; 9 - ерозия зона; 10 - катода - мишена
Директно под целта има постоянни магнити, които създават по същество успоредно на повърхността на магнитното поле на катод. Между анода и катода отговорност газ се запалва ненормално. В резултат на това електроните се почука на катода, които са заловени от магнитното поле, и правят това поле под действието на силата на Лоренц спираловидно движение. Електроните капан магнитно поле, се извършва допълнително йонизация на инертни газове, които атоми увеличава, като по този начин, интензитетът на йонно бомбардиране на катодната повърхност и по този начин води до увеличаване на скоростта на разпръскване.
Основните характеристики на взаимно определяне на целевата скорост разпрашаване, включват освобождаване на напрежението, разряден ток, налягането на работния газ и индукция на магнитното поле в близост до повърхността на катода. Работната газ в разпрашаване системи магнетронни често се използва аргон.
Магнетронно разпрашване системи, различни от високата скорост имат редица специфични характеристики, основната от които е липсата на високо-енергийна бомбардиране на субстрата от вторични електрони е основен източник на радиация дефекти в покритието и нагряване на субстратите. Системата за магнетронно разпрашване, вторичните електроните се улавят от магнитен уловител и бомбардиране на субстрата, че тя осигурява с относително ниска температура. Това позволява използването на тези системи за покривни повърхности, изработени от материали с относително ниска устойчивост на топлина (пластмаси, полимери, хартия).
Трябва да се отбележи, че магнетрона на системата са слаботокови системи за нанасяне на покрития, които захранващото напрежение не превишава 1000 V DC. Работното напрежение е типично 300 ... 700 V; за целта обикновено се сервира отделно потенциал и потенциала за анод е нула. Магнетронно система може да работи в обхвата на налягането 10-2 до 1 Pa или по-висока. Най-важните параметри, които определят до голяма степен отговорност характер него е геометрията на електродите и магнитната индукция на полето на повърхността на мишената, която
процес магнетронно покритие характеризира със следните параметри:
-Скорост спрей - (4 ... 40) · 10-5 г / (cm2 · S);
-покритие отлагане Velocity - 50 ... 60 нм / сек.
-специфичен изпаряване - β≈3 · 10-6 г / J..
- енергията на бомбардирани частиците - 10 ... 20 ЕГ.
Предимствата на този метод в сравнение с други методи на покритие:
1) с висока скорост на отлагане;
2) почти пълното отсъствие на прегряване повърхността на детайла, докато електрони са хванати в магнитното поле и затова не предизвиква образуването на радиационни ефекти;
3) равномерен покрития;
4) ниска степен на замърсяване филми, т. К. процес на нанасяне на покритие се извършва в р достатъчно ниско налягане = 10-2 Ра.
През последните години активно разработен от реактивен магнетронно разпрашване. В изпълнението им има редица технологични характеристики, които трябва да бъдат взети под внимание. При пръскане целева част от реактивни газове пулверизира свързва вещество, и част - непрекъснато подновяване на повърхността на мишената. Това е един вид изпомпване реактивен газ. На този принцип, както знаем, на базата йонна кариерист вакуумни помпи. Скоростта изпомпване зависи от зоната на пулверизиране на отложените покрития, скоростта на растеж на целевата зона, скоростта на отделяне на образуваната върху мишената и се проявява в рязък спад в налягането на газа в реактивната камера с началото на процеса на пръскане филма.
Когато реактивна скорост на растеж покритие магнетронно разпрашване зависи от парциалното налягане на реактивен газ. При ниски налягания на реактивен газ разпръсква от целевата метал и химична реакция се появява върху субстрата. При по-високи налягания, при целевата повърхност се образува от съединение филм химически и разпрашаване процент пада рязко защото скоростта пръскане химични съединения (оксиди, нитриди, карбиди) е значително по-ниска от чисти метали. За да се намали този ефект редица устройства, разработени в който подаването на реактивен газ се извършва директно върху субстрата, и инертен - на мишената за разпрашаване (Фигура 5).
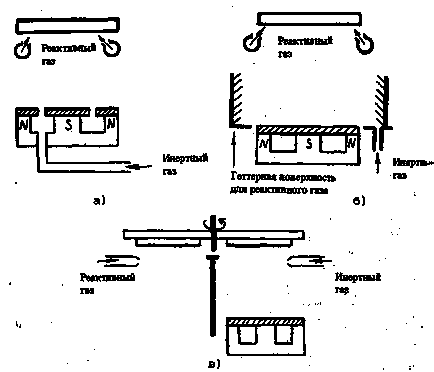
Фигура 5 - схема на устройството от реактивни области на разделяне магнетронно разпрашаване намирането инертни и реактивни газове, и - чрез селективно доставяне на газ; б - с приемателното повърхност; в - чрез преграда и относително движение на субстрата
Устройства също са разработени, в които йонно разпрашване и процеси термично изпарение са комбинирани в един процес спрей изпаряване. Това се постига, например, чрез магнетронно разпрашване материал в течно състояние. В този случай, производителността на процеса е значително подобрена пулверизиране и използването на целевия продукт. Това се дължи на факта, че разпрашване процес протича в метален повърхностен слой на 0.3 дебелина. 0.8 пМ, и консумират по-малко от 3% от доставя енергия. Останалата част от енергията се превръща главно в топлина, така че целта трябва да се охлажда бързо. В устройства, проектирани енергия, която се губи под формата на топлина в спрей от твърдата фаза, се използва за изпаряване на вещества.
За този процес между плоската тигела, изработен от огнеупорен немагнитен материал и вода охлажда магнитна система направи малка (2-3 mm) междина, която позволява топлинно излъчване от тигела през разпрашване цел поставя в тигел (Фигура 6).
Фигура 6 - схема на устройството за пръскане фаза материали течни: 1 - тигел; 2 - разтопен цел; 3- анод; 4 - на екрана; 5 - магнитна система; 6 - носителят на субстрат
Работният обем се евакуира, аргон след това нека в и между тигела, който действа като се прилага мишена и анод напрежение, постепенно увеличаване на плътността на тока в целта до стойност, при която започва интензивно топене материал намира в тигела. Когато това се топи първата зона, в която локализиран плазмата, а след това - в централната част на целта и накрая си край област. В определен плътност на тока на целта започва интензивно изпарение на материала на стопилка. При достигане на високо налягане на парите на разпръсква материал започва процеса на самостоятелно разпрашаване на катода. В този случай, може да спре плискане на аргон, което значително намалява замърсяването с остатъчен газове филм. В допълнение към висока енергийна ефективност, системата срещу изпарител дава възможност за постигане на високи скорости на отлагане.
С цел да се подобри адхезията на покритието към субстрата се подава, обикновено, отрицателен потенциал отклонение
100 V, като по този начин повишаване на енергийната плътност и йон.