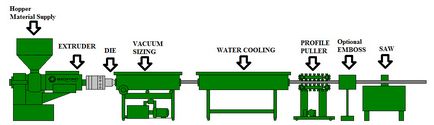
Около половината изработен от термопластични материали се преработват в продукти по този начин. Екструзия получава филми, листове, тръби, маркучи, капиляри, пръчки, обшивка, различни профили сложност прилагат полимер изолация на проводниците, които произвеждат различни многослойни конструкции и хибридна комбинация използват пластмасови отливки. Полимер рециклиране и гранулиране се извършва също с помощта на оборудване екструзия.
Основното оборудване на процеса на екструзия е екструдер, снабден с глава формиране. В екструдера, полимерният материал се разтопява, пластифицира и след това се инжектира в матрицата. Най-често се използва една и различни модификации двушнеков екструдер.
Понякога, когато се използват пластмаси besshnekovye или дискови екструдери, в която работи тялото е екструдиран стопилка в главата, това е специална форма на диск. се използват, когато е необходимо дискови екструдери за да се получи подобрено смесване на компонентите на сместа. Поради невъзможността да се разработи високо налягане, формоване такива екструдери се използва за производство на продукти с относително ниски механични свойства и малка точност геометрични размери.
Комбинирани екструдери са работещи устройство съвкупност винт и част диск, и червей нар диска. Те се използват за осигуряване на добро смесване ефект, особено при обработката на композити. Те стопилка обработват пластмаси с нисък вискозитет и достатъчно висока еластичност.
Процесите, които се провеждат по време на екструзия.
Фиг. Схема 1. единично винтов екструдер: 1- бункер; 2- винт; 3- цилиндър; 4- кухина за циркулиране на водата; 5- нагревател; 6- решетка мрежи; 7 глава форма.
процес екструзионен процес се състои от последователно движение на материал въртящ се винт в неговите зони (виж фигура 1 ..): Мощност (I), сдъвкване (II), стопилка дозиране (III), и след това стопилката настъпващите канали, образуващи глава.
Разделяне винта към зона I-III се извършва на база мрежата и показва какво операция основно изпълнява тази част винт. Зоната за разделяне на винта за условно, тъй като, в зависимост от природата на полимера се обработва, температурата и скоростта на условията на процеса и други фактори на началото и края на специфични операции може да се премества по дължината на винта, улавяне различни зони или преминаване от едно място на друго.
Цилиндърът също има определена дължина на нагревателни зони. Дължината на тези зони се определя от разположението на нагревателите на повърхността си и неговата температура. Границите I-III на зоните на винт и барел нагревателни зони могат да бъдат различни.
Ние считаме, че поведението на материала последователно върху всяка стъпка екструдиране.
суровина натоварване. Суровината за екструзия, се подава в резервоара може да бъде под формата на прах, гранули, ленти. Единният дозиране на материала от бункера осигурява добро качество екструдиран.
Рециклиране на полимера под формата на пелета - най-добрия режим на мощността на екструдер. Това е така, защото полимерните гранули са по-малко склонни към образуване на "купол" в бункера от праха, следователно, пулсациите на потока се елиминират на изхода на екструдера.
Зареждане interturn пространство под фунията за силоз се извършва при дължина на винт интервал равна на (1 - 1,5) D. В образуването на "Кодекса" по стените на шнека силоз спира храна материал. За да се преодолее това, което трябва да се сложи в стругари на бункера.
Течливостта на материала зависи до голяма степен на влажност по-висока влажност, по-малко течливостта. Поради това, материалът трябва първо да се печените.
За да се увеличи производителността на пелети Машината може да бъде предварително загрята.
Използване на устройството за сила хранене материали от бункера на шнека, също успява значително да се подобри ефективността на машината (3-4 пъти). Когато уплътняване на материала в interturn пространство на винт разселени въздух напуска обратно през бункера. Ако отстраняването на въздуха е непълна, а след това той ще остане в стопилката и формовани кухина образува продукт, който е омъжените продукти.
Промяна на височината на нивото на запълване на бункера материал се отразява и пълнотата на винта. Ето защо, бункерът е осигурена със специално автоматично габарити, което се случва при зареждане бункера на терена материал до желаното ниво. Зарежда бункера на екструдера се извършва с помощта на пневматични пренасяне.
В непрекъсната работа на екструдер може да прегрее цилиндър под бункера и бункера на бункера. В този случай, гранулите започват да се държим заедно и да се спре потока им към шнека. За да се избегне прегряване на кухината на цилиндър, изработен в него за циркулация на охлаждаща вода (вж. Фиг. 1, поз. 4).
фураж зона (I). гранули, идващи от interturn пространство зона бункера запълване свредел аз и се уплътнява. Запечатване и пресоване на гранулите в областта I се случи, обикновено чрез намаляване на дълбочината на рязане Н винта. Насърчаване на гранули, направени поради стойностите разлика на триене сила на полимера върху вътрешната повърхност на тялото на цилиндъра и повърхността на винта. Тъй като повърхностен контакт полимер с повърхността на винта е по-голяма от повърхността на бутилката, е необходимо да се намали коефициента на триене полимер на винта, защото в противен случай материала ще престане да се движи по оста на винта и ще се завърти с тях. Това се постига чрез повишаване на температурата цилиндър стена (отопление) температура и завийте (шнек охлажда вътрешно с вода).
Отопление на полимера в зона I се дължи на разсейване топлина от триене материал, и в резултат на допълнителна топлина от нагревателите, разположени по обиколката на цилиндъра.
Понякога количеството на разсейване на топлината може да бъде достатъчно, за да се стопи полимера и след спиране на нагревателите. На практика това се случва рядко.
В оптималната температура на процеса на полимер уплътнява, уплътнява и образува твърда маса в пространство interturn (вж. Фиг. 2). Най-добре е, ако се формира тази плъзгащи тръба и се съхранява на границата на зони I и II. Tube свойства голяма степен определят производителността на машината, стабилност транспортиране полимер, максималната стойност на налягането, и така нататък. Г.
Фиг. 2. Тръбна материал топене на Схема зона II сечение в interturn винта: 1- стена на цилиндъра; 2- винт ръб; 3- полимерната стопилка потоци; 4- уплътнен твърд полимер (тръба) в екструдера.
пластифициране и топене зона (II). В началото на зона II submelting полимер настъпва съседната повърхност на цилиндъра. Стопилката постепенно се натрупва и се отразява на намаляване на ширината на тапата. Тъй като дълбочината на рязане на винта намалява един движи материал от зона I към зона III, в резултат на налягането предизвиква щепсела здраво притиснат към горещата стена на цилиндъра, полимерната стопилка се случи.
В топи plastication зона тръба и под въздействието на топлина, генерирана в резултат на вътрешно вискозно триене в материала, за да се стопи тънък слой (поз. 3 на фиг. 2), където интензивно срязване деформация срещащи. Последното обстоятелство води до смесване изразен ефект. Стопилката се хомогенизира интензивно и компонентите на композитния материал се смесват.
Крайната зона II се характеризира с разпадането на отделни парчета тръба. Освен това, полимерът се стопи с останки частици влиза измерване зона.
P покачване основната стопилка налягане настъпва при границата на зони I и II. Тази граница се образува слой от пресован материал, докато се плъзга върху винта: в зона I е твърд материал в зоната на топене II-. Наличието на този задръстванията и създава съществен принос за налягането на стопилката. Също повишаване на налягането се случва за сметка на намаляване на дълбочината на рязане на винта. Съхраняван на изхода на налягането на цилиндъра, се използва за преодоляване мрежа резистентност, каналите за стопилка в главата и на продукта за формоване.
дозираща зона (III). Насърчаване на хетерогенен материал (стопилка, твърди полимерни частици) продължава да се придружава от освобождаването на вътрешния топлинна енергия, което е резултат от интензивно срязване щам в полимера. Стопената маса продължава да се хомогенизира, което води до крайна топене на твърдите полимерни остатъци средно вискозитет и температурата на стопения част.
В interturn пространство има редица стопилка потоци, основните от които са надлъжно и кръвообращението. Големината на надлъжните (по протежение на оста на винта) на екструдера определя ефективността на Q на потока, и кръвообращението - хомогенността или качеството на смесване на компонентите на полимера.
На свой ред, надлъжната поток се състои от три стопилка потоци: напред, назад поток и изтичане.
Директен дебит, причинени от движение на винта по посока на формиращата глава. Обратен поток - въображаем ток, поради високото налягане от главата; в действителност не съществува. изтичане на потока става при препълване стопилка между цилиндъра и гребен винт.
Изход Q на екструдера с разпределението на скоростта на различните потоци е
Q = QPR - Qobr - Qut,
където QPR, Qobr, Qut - изпълнение на екструдер надолу и стопи изтичане обратен поток съответно.
Q = αn - β • (АР) / (μ • L),
където п - честотата на въртене на шнека; АР - налягане на изхода на винта (в края на зона III); μ - ефективното вискозитета на стопилката; L - дължина на винта; α - директно постоянен дебит, β - постоянна скорост обратен поток, което зависи от геометричните параметри на винта.
Основните параметри на процеса на екструзия. За параметри на процеса включват температури на обработка полимер, стопи налягане, умират температурни зони температурата и охлаждане режими на формован екструдата.
В твърде висок вискозитет на стопилката за производство на изделия чрез екструзия трудно поради висока устойчивост, се стопи поток, поява на режима на нестабилна поток. Всичко това води до образуването на дефекти на продуктите.
Увеличаване температури обработка може да доведе до термично разграждане на стопилката и повишаването на налягането, мощността на задвижване при ниски температури - за механично разграждане, т.е. екструдиране на стопилка трябва да се прилага полимери с относително тесен интервал колебание вискозитет.
Основните характеристики са едновинтов екструдер, L, D, L / D, винт скорост п, геометричната профил на винта (виж фигура 3). И компресия (натиск) - съотношение на обема на един оборот на шнека в зоната на подаване на обема на една линия в зоната дозиране.
Фиг. 3. Шофиране винт банда структура
Korotkoshnekovye екструдери имат L / D = 12-18, dlinnoshnekovye L / D> 30. Най-често екструдера с L / D = 20-25.
Индикация за екструдер е неговата effektivnost- съотношение на производителност на консумацията на енергия.
Материали. Повечето термопластични и техни състави могат да бъдат обработени чрез екструзия. Достатъчно е, че времето за пребиваване на стопилката в екструдера при тази температура е по-малко време термична стабилност на полимера при същата температура. Най-често използваните екструзия насипни полимерите от следните видове. PE, PP, PS PA PC, PVC (пластифицира и непластифициран), PET и техни смеси с неорганични или полимерни ексципиенти и по-сложни състави на тяхна основа.
Материалите, използвани за екструзия и обработка на режимите, при което MFR варира в рамките на 0,3 - 12 гр / 10 мин, защото на нисковискозна топи невъзможно да се получи непрекъсната екструзия заготовки във филм, тръби, профил. Ако се използват за леене под налягане степените на полимер, или те могат да бъдат екструдирани само определени видове продукти, тъй като те имат MFR е в диапазона 0.8 - 20 г / 10 мин.
Така, тръби, кабелни покрития, направени от полимерна стопилка MFR от 0,3 до 1 г / 10 мин. Това се дължи на избора на полимер с високо молекулно тегло. Последното определя експлоатационните характеристики на продукта - увеличаване на физико-механични характеристики.
Филми, листове са направени с екструзия на стопилка MFR в границите от 1 - 4 грама / 10 мин.
Дискретни продукти, произведени чрез екструзия, последвано от формоване чрез раздуване в една форма се получава от стопилка MFR = 1.5 - 7.0 грама / 10 мин.
Ламиниране чрез екструзия с MFR стопилка настъпва в рамките на 7-12 г / 10 мин.
Продукти. Всички продукти са произведени на базата на термопласти чрез екструдиране може да има принцип неограничена дължина. Диаметър на продуктите се ограничава главно диаметър на винт екструдер. D. Колкото по-широк, могат да се получат по-дебели продукти.
На този сайт: полимерни материали
навигация в публикациите