При производството на по-голямата част от детайлите, необходими за да се справят дупките. Отворите могат да бъдат както типични част функции, и се използват, например, за поставяне на скрепителни елементи, да бъде или задействане повърхности, върху които има двойка части в механизма, или да служи като канали за предаване на флуиди или газове. По този начин, в зависимост от изискванията за дестинация за услуги за точност и качество на повърхността, може да варира значително. Най-важният параметър влияе върху избора на дупка машинна технология, е съотношението на дълбочина диаметър. В модерния метал се счита за плитки дупки, ако съотношението не превишава 5. За обработката на такива отвори, без никакви ограничения могат да се прилагат всички видове пробиване и довършителни край и скучен инструмент. В същото време дълбоко еднозначно отнасят дупки с дълбочина съотношение диаметър по-голям от 20. Необходимо е да се използва специализирана техника и инструменти за пробиване на дълбоки дупки и скучен, функцията отличителния е наличието на водещи елементи за поддържане на режещата част на стената на машинно дупката. Съответно, гама от междинно съединение дължина съотношения диаметър може да се използва с някои ограничения като удължени версии на конвенционални инструменти и средства за дълбок отвор обработка. Всяка една от тези системи, показва най-висока ефективност в редица диаметри и сондажни дълбочини.
Пробиване и райбероване
Най-често срещаният метод за производство на отвори в твърдия материал е пробиване. рязане движение при пробиване - върти, движението на животните - транслацията. Преди да започнете, проверете съвпадането на върха на предната и задната част на центровете на машината. Заготовката се поставя в патрон и проверява, че неговата биене (ексцентричност) спрямо оста на въртене не надвишава допускане под външната смилане на субекта. Проверете биене края на детайла, в които дупката да бъдат обработени, и се проверява от края на детайла с лицето. Перпендикулярна на края на оста на въртене на детайла може да се осигури с лице, в центъра на детайла може да се направи куха за желаната посока на тренировка и да се предотврати неговото оттегляне и счупване.
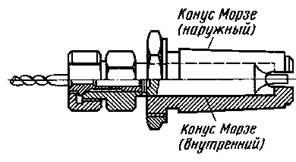
При пробиване на отвор, дълбочината на която е по-голяма от нейния диаметър, свредлото периодично изведена от обработвания отвор и се пречиства жлеб отвор свредлото и заготовката от натрупаните чипове. За да се намали триенето на инструмента стената отвор на сондажа се провежда с подаване на охлаждащата течност (рязане течност), особено в обработката на стоманени или алуминиеви заготовки. Чугун, месинг и бронз детайла могат да бъдат пробити без охлаждане. Използването на охлаждащи течности може да се подобри скоростта на рязане на 1,4-1,5 пъти. Както се използва разтвор на охлаждащата течност на емулсията (за структурни стомани) съставени масла (за легирани стомани), разтвор на емулсия и керосин (за чугун и алуминиеви сплави). Ако машината не е предвидена за охлаждане на охлаждащото средство като смес от смазочно масло и керосин. Прилагане на охлаждащата течност да се намали аксиални и тангенциални режещи сили от 10-35% при пробиване стомани 10-18% при пробиване чугун и цветни сплави, и 30-40% в сондажни алуминиеви сплави. Когато сондиране за удължаване на времето на тренировка от детайла трябва да доведе до рязко намаляване на потока да се предотврати счупване на тренировка. За сигурността на сондажния инструмент трябва да се работи с максимално допустимата скорост за рязане и на най-ниското допустимо поток. Ако оста на тренировка съвпада с оста на шпиндела на струга, бормашина наточени правилно и се фиксира неподвижно, обработвания отвор е с минимална грешка. Ние работим правилно заточени тренировка два режещи ръба и чип в две винтови нарези. Измерванията се получават при пробиване на отвори по-голям набор от следните случаи: свредлото режещи ръбове са с различни дължини, въпреки заточени на равни ъгли; режещи ръбове са с различна дължина и заточени под различни ъгли; режещи ръбове са с еднаква дължина, но изострени ъгли. Когато наточени правилно и при наклонен сондаж се получава с голяма грапавост. Освен това, когато заострения достатъчно (тъп) бормашина дупка в изходната част са оформени грапавини. В различна дължина и не-симетрични режещите ръбове на заточване, ексцентричната подреждането на различни ширина платна и ленти причиняват смущения на свредлото в отвора, което увеличава силата на триене (задълбочаването на свредлото в детайла) и, като следствие, води до счупване на инструмента. Обработена наречена дълбока дупка, ако дълбочината му е 5 пъти по-голяма от диаметъра му. Когато пробиване дълбоки отвори използвани дълго обрат тренировка с конвенционални геометрични параметри, които периодично се извеждат от третираните охлаждащи отвори и отстраняване на натрупаните чипове в жлебовете. За да се подобри ефективността обработка на свредлото се използва с принудително отнемане на чипове провежда при използване на течност (или въздух) се подава под налягане в зоната на рязане.
С увеличаването на пробиване дълбочина на свредлото влоши работните условия, се влошава отвеждане на топлината увеличава триенето на чип стена на жлеба на инструмента, е затруднено охладител на режещите ръбове. Ето защо, ако дълбочината на пробиване повече от три пъти диаметъра на обработвания отвор, скоростта на рязане трябва да бъде намалена. За пробиване на отвори, използвани обрат тренировки, които са изработени от инструментална стомана (въглерод и сплав 9HS U12A) на висока скорост стомани (R6M5 и др.), И е изработен от твърд метал (VK6M и VK8M VK10M). За бормашини с висока скорост скорост стомана рязане U = 25-35 м / мин, за пробиване на инструментални стомани ф = 12-18 м / мин, за карбид тренировки ф = 50-70 м / мин. Освен това, високи стойности на скорост на рязане, взети като диаметъра на свредлото и намаляване на захранване. Когато ръчно подаване пробиват трудно е да се осигури постоянна (стабилна стойност). За да се стабилизира фуража се използват различни устройства. За храната механичното тренировка го фиксира в държача. Пробивната коронка 1 с цилиндрична опашка, фигура snizuleva - а) с ограничителите 2 и 3, монтиран в държача така, че оста на тренировка съвпада с линията на центрове. Пробивната коронка 1 с конусна опашка, наляво чертежа - б), монтирани в държача 2, която е фиксирана в държача.
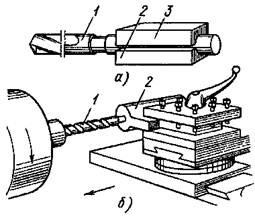
След изравняване съвпадение тренировка Caliper централна ос линия с бормашина ръчно подава към края на отвора на детайла и се обработва с минимална дълбочина тест, а след това да включва механичен шублер фуражи. Когато добив на преминаване преди излизане на свредлото от детайла механична храненето значително намалена или отрязани и край обработката на ръка. При пробиване на отвори с диаметър 5-30 mm стъпка S = 0, Ь-0,3 мм / об за стоманените части и S = 0,2-0,6 мм / обороти за чугунени детайли. Рязане при пробиване има редица функции в сравнение с обработка по време на завъртане, тъй тренировка обрат - многоперков инструмент, който изпълнява рязане с пет режещи ръбове (две първични, вторични и две напречни).
Когато пробивате дупки като тренировка износване на задната повърхност на осовата сила и въртящ момент се увеличава; например, по време на носене на задната повърхност на сондажния 1 тМ тези параметри увеличава почти 60-80%. За да се подобри ефективността на обрат тренировки, използвайки техники като изтъняване на напречните ръбове, промяната на ъгъла на лентата на връх изтъняване, двойно ръб, преди райбероване дупки и др. Типични тренировки имат ъгъл връх 118 градуса, обаче, за обработка на трудни материали (и по- дълбока дупка) се препоръчва да се използва сонда с ъгъл при върха на 135 градуса. Форми заточване на режещата част на инструмента, показан на фигурата по-долу.
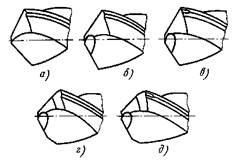
а) - нормални, Ь) - нормален изтъняване платна, с) - от нормални изтъняване платна и ленти, г) - скок изтъняване двойно, г) - двойно скок изтъняване и ленти
Boring осигурява по-точни дупки и намаляване на оттеглянето на тренировка от оста на детайла. С пробиване на отвори с голям диаметър (повече от 25-30 мм), силата на храна може да бъде прекалено голяма. Затова в такива случаи, сондажите се извършва на няколко етапа, т.е.. Д. Hole купища. рязане условия за пробиване на отвори същите, както при пробиване. Фигурата отляво елементи рязане по време на пробиване и) и пробиване - б) на отвора: п - въртене на свредлото, Sz - емисия на един режещ ръб, а и б - ширината и дебелината на слоя на срязване, т - страничен помощ, D - диаметър главния отвор, До - диаметър предварително пробит отвор
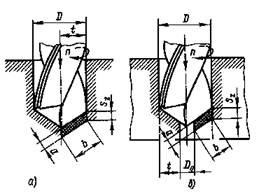
Райбероване и внедряване
Райбероване. Зенкери дупки са лекувани преди това подпечатани, излети или пробити. Рисуване - а). Зенкероване под квоти (след пробиване) е 0,5-3 мм за страна. Зенкери избира в зависимост от материала, който се обработва, формата (чрез, пристъпи, сляпо), а диаметърът на отвора и предварително определена механична точност. Зенкери има три или повече режещи ръбове, така отстраняват под райбероване и тънки чипове са по-точни отвори, отколкото по време на пробиване; тя е по-силна, отколкото на тренировка, така че ядрото на доставките пробиване на 2.5-3 пъти скоростта на захранване за пробиване. Зенкероване може да бъде или предварително (преди разгръщане), както и окончателната операция. Освен зенкери машинни дупки, използвани за обработка на крайните повърхности. За да се подобри точността зенкероване (особено в преработката на гласове или щамповани дълбока дупка) се препоръчва да се длето (длето) отвор с диаметър, равен на диаметъра на фаска на дълбочина приблизително равна на половината от дължината на работа част от фаска. За обработка на материали с висока якост (SRE> 750 МРа) се използват зенкери оборудвани с плочи от твърд метал. Скорост на рязане за основните тренировки HSS е същата, както за тренировки. Скоростта на рязане на карбид райбери са 2-3 пъти по-голяма от високоскоростен стомана зенкер. При обработка с висока якост материали и формоване на кора скорост на рязане карбид зенкер следва да се намали с 20-30%.
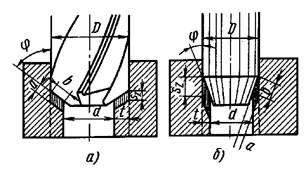
Внедряване. За отвори с висока точност и качество на обработваната повърхност се използва за разполагане. Рисуване - б). Scan има много по-авангардни от зенкер, така че разполагането се отстранява тънки чипове и са по-точни дупка, отколкото когато райбероване. диаметър дупки 10 мм е разположена веднага след пробиване. При внедряването на по-големи отвори с диаметър от предварително обработена и почистена край. Прибавка за разполагане т = 0,15-0,5 мм за грубо райбери и 0.05-0.25 mm за довършителни сканиране. Когато Завършени скан-стругове и стругове, Стругове, използвани люлеене дорник, който компенсира несъответствието с оста на дупките сканиране ос. За да се осигури високо качество на обработка, пробиване, зенкероване (или пробиване) и разполагането на отворите произведени за единица на машината детайла в патронника. Емисия за разполагане на стоманени части 0,5-2 мм / об и чугунени части в разполагането на 1-4 мм / об. Намаляване на скоростта разполагане на 6-16 м / мин. По-големият диаметър на обработвания отвор, долната скорост на рязане в същото терена, докато увеличаване скоростта на подаване на рязане намалява.
Ако диаметърът на отвора надвишава диаметъра на стандартни бормашини или райбери, като дупка отвор. Boring се прилага и при обработката на огромни дупки с неравномерно или не-праволинейна образуваща. Включване разширяващи фрези за обработка чрез - а) и глух - б) отвори са показани по-долу. При завъртане прът разширяващи ножове, на чертежа) и г) се извършват в частта на рамото кръг и прът служи за закрепване на инструмента - квадрат (12x12, 16x16, 20x20 и 25x25 mm); такива ножове могат сонди с диаметър 30-65 мм. За да се подобри устойчивостта на вибрациите на инструменти за рязане на режещия ръб, носени от оста на прът, фигура г) и д). На шпил машини, използвани скучни резачки кръгло сечение, които са монтирани в специален държач инструмент, фигура г). Форма на предната повърхност и всички краища имат скучни резачки, с изключение на задната, се правят същата като тази на втулката за целите на външната повратна. Заден ъгъл на<12 градусов при растачивании отверстий диаметром более 50 мм и a>12 градуса, когато пробивни дупки с диаметър по-малък от 50 мм. Стойността на ъгъла на рязане в разширяващи ножове може да се променя чрез настройване на острието на режещия ръб по отношение на надлъжната ос на част (над или под оста). Когато скучно инструмент се намира в по-тежки условия, отколкото във външната надлъжно завъртане; като влоши условията за отстраняване чип, охладител и отвеждане на топлината. Boring титуляр нож има по-малко сечение и по-голяма катастрофа, която причинява нож предене и допринася за вибрациите; обаче когато ПРОБИВНИ обикновено отстранява минимална точка чип и намалена скорост на рязане. Когато груб пробиване рязане на стомана като дълбочина 3 mm; 0,08- надлъжната храна 0.2 mm / об; скорост на рязане от около 25 м / мин за скорост стомана режещи инструменти и 50-100 м / мин за карбид нож. Когато фин пробиване дълбочина на рязане не надвишава 1 mm, дължината на фуража 0,05-0,1 мм / об скорост на рязане 40-80 м / мин за скорост стомана режещи инструменти и 150-200 м / мин за карбид нож.
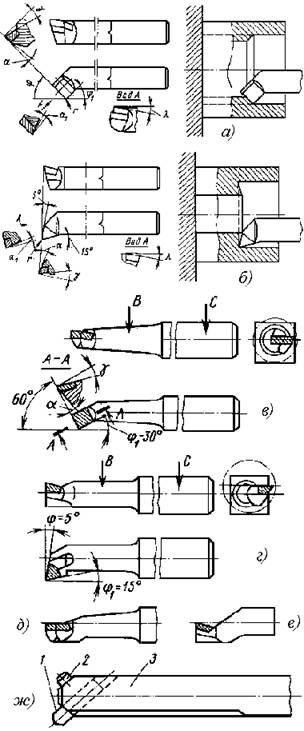
нарязване на резба дупка монтаж
Свързани статии