За да се получи желаният продукт минерали се обработват в трошене и пресяване растенията.
Обработка се състои от раздробяване, пресяване, измиване и обогатяване Чакъл, чакъл, пясък.
Раздробяване и смилане - намаляване на размера на рок масови парчета от механично унищожаване. Смята се, че по време на продукти фрагментация получен главно голям и смилане е по-малка от 0.5 mm. Дробилка използва за раздробяване и смилане на мелницата.
Сортирането (скрининг) - отделяне на преработени продукти от размера на екраните.
Измиване чакъл и чакъл се извършва за да се отстранят Komkova глина, тиня и глинести частици. Пералня може да се извършва на екрани или в автомивка.
Класификация и обогатяване на пясък се използва за регулиране на състава на зърното на държавните стандарти. Тези операции се извършват в gidroklassifikatorah и концентриране апарати (хидроциклони).
Обогатяване на трошен камък и чакъл сила извършва в седиментни машини, механични класификатори, инсталации за обогатяване на тежка медии.
Обогатяване каменните оформени зърна са предназначени за чакъл правоъгълен паралелепипед форма. Тази операция се извършва селективно сортиране на отвори сито гранулиране чакъл в ротационни ударни мелници и гранулатори в барабани.
За да изберете технологичната схема на преработката на минерални суровини, трябва да имате следните данни:
- характеристики на оригиналния скалните маси;
- Сила и зърнеста структура;
- гама от готова продукция.
Способността на скалата, за да устои на разграждане зависи от силата, наличието на пукнатини в парчета, средствата за излагане на разрушителни сили. Най-голямото съпротивление са рок раздробяване, по-малко - огъване и особено разтягане.
При избора на технологичната схема на производство се вземат предвид вида на преработени рок (фиг. 7.2.1).
I - хомогенна вулканична скала с якост на 600 МРа или повече, метаморфен (утайка) натиск скали със силата на 60-250 МРа;
II - твърди хомогенни утайки с якост на натиск 60-200 МРа;
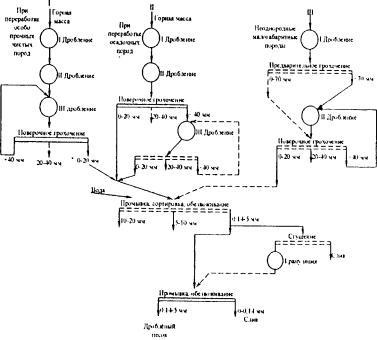
Фиг. 7.2.1. Технологична схема за раздробяване, пресяване, измиване
Количественият характеристика на процеса на смачкване е степента на раздробяване, показва колко пъти парчета материал се намалява по време на раздробяване.
С степента на фрагментация, свързани енергийните разходи и изпълнението на трошачки.
където Dmax - най-големият диаметър на парчето на раздробяване;
Dmax - най-големият диаметър на парче и след смачкване.
За конкретни трошачки, съдържащи се в информационните листове за изходни класове графика чакъл в зависимост от ширината на трошачката изходящия процеп за конвенционално приета рок плътност.
Например, за да се получи чакъл 20 mm размер парче когато подава към трошачката 600 mm аз = 600/20 = 30. Това означава, че е необходимо да смаже парче 30 части.
Получаването на такива високи степени на трошене в трошачка е практически невъзможно, тъй като всяка мелница работи само с ограничена степен на раздробяване. Рационално материал от по-голямата до желаното разделяне в няколко последователни мелници (Фиг. 7.2.2).
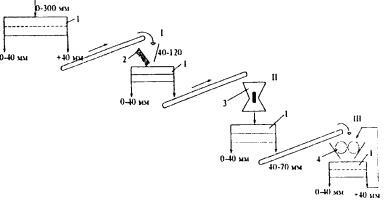
Фиг. 7.2.2. Три етап смачкване схема:
1 - рев; 2 - челюстна трошачка; 3 - конусна трошачка; 4 - трошачка; I, II, III - стъпка смачкване
Степента на сплескване, получена във всяка стъпка, по-нататък частни, във всички етапи - общата степен на раздробяване.
Материалът въвеждане на смилане, винаги има по-малки парчета с размер, който е разделен, с тази стъпка. Тези части са изолирани от изходния материал в съответствие с принципа "фракция не нищо допълнително." Crusher може да се управлява в отворени или затворени цикли. Смленият продукт се подава към трясък, освобождаване от тях големи парчета се връщат за повторно трошене еднакви, или вторична трошачка (Фиг. 7.2.2).
Паспорти фабрика - водят до производството на скални трошачки средна плътност от 1600 кг / м 3 и при условие, че размера на най-големите парчета от Dmax трябва да бъде по-малко от 0.8. 0.9 от ширината на трошачката за откриване на запълване. При проектирането и избора KDZ ротърни тяхното производство се вземат предвид физико-механични свойства на скалата. Изчислено за изпълнение челюстни трошачки експериментално определени от формула
където Рр - производство паспорт т / час;
Kd - разбие скала фактор (за дъскорезници с крайната натиск sszhat = 150. 250 МРа - 0.9, и за средни породи legkodrobimyh sszhat = 50. 150 МРа - 1.1-1.2);
KG - коефициент това, насипна плътност от натрошен материал (KG = г / г GP - насипна плътност на раздробения материал ;. Gp - насипна плътност, съответстваща данни сертификат);
Kf - коефициент, отразяващ формата на камъка Kf = R / 1.6 (или 1.0 при парцалива камък смачкване, 0.85 - когато смачкване камък чакъл-маса);
KCR - коефициент, отразяващ степента на трошен материал.
Степен на натрошен материал KCR
0.85 трошачка гърлото ширина 1.00
0.60 трошачка гърлото ширина 1.07
0.40 трошачка гърлото ширина 1.16
0.30 трошачка гърлото ширина 1.23
Също изчислява също така е възможно да се използва изхода на Оценката, която обикновено се посочи минималната и максималната широчина на смачкване празнината.
Дробилка ширина междина, при която се достига предварително определен капацитет, се определя по формулата
където Dmin - минимална ширина на смачкване разликата, мм;
Pmin - Dmin изпълнение трошачка. м3 / ч;
Dmax - максимална широчина на смачкване празнина, мм;
Pmax - трошачка Dmax производителност. m 3 / час.
Промяна на ширината на смачкване разликата влияе върху ефективността на трошачката и степента на смилане материал. С увеличаване на ширината увеличава производителността и намалява степента на смилане и намалява добива на техния размер.
Приблизителни добив чакъл фракции след смачкване в зависимост от ширината на междината трошачка могат да се определят от кривите на разцепване (Фиг. 7.2.3).
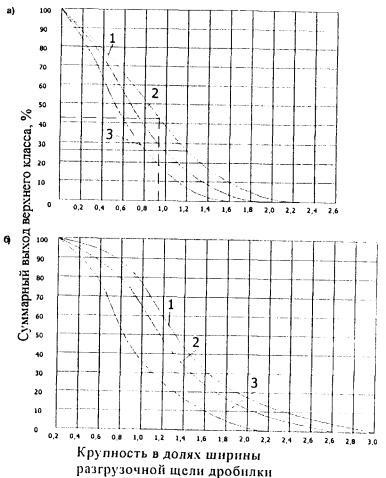
Фиг. 7.2.3. трошене криви
и - челюстна трошачка; б - конусна трошачка; 1- дъскорезници за сила повече от 150 МРа, 2 - рок сила на 80-150 МРа; 3 - рок сила МРа 30 80
Тези графики изясняване на резултатите от работата на трошачки на дизайна, размерите им, като се вземат предвид свойствата на трошен камък. При определяне на максималния размер на материала по кривите трябва да се забравя, че при конвенционален максимален размер на зърната на раздробената продукт предполагаемо размер на ситото, чрез който 95% от материала преминава.
За визуално представяне на процеса на работа смачкване растения развиват количествен и качествен раздробяване верига (Фиг. 7.2.4).
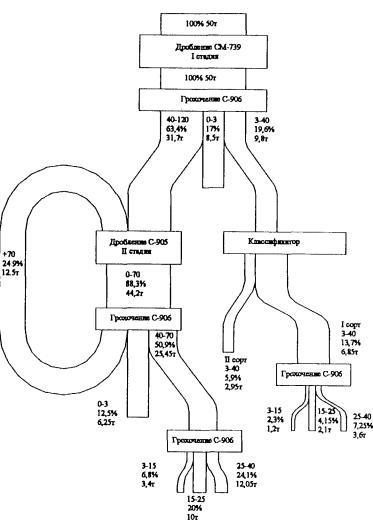
Фиг. 7.2.4. Количествен и качествен смачкване верига
Количествено диаграма показва колко и в каква последователност вход на процеса и на растителния материал, тъй като преминава отделните операции на процеса. Количественото верига може да бъде оформен на базата на тонажа или обема на обработвания материал. В този случай е необходимо да се вземе под внимание, че обемът на материал, получен от трошене и пресяване, ще надвишава сумата от изходния материал. Увеличението се определя чрез увеличаване на коефициента на обем от 1.1. 1.25. Количествено диаграма показва количеството на обработвания материал (обем, маса, процент) на отделен процес сайтове.
Качествена верига съдържа фракция с размер на данни, процесът на режим материал и обработка на избрани места. Апарати схема диаграма, показваща начина на следния материал по време на обработка на данни и устройства, които изпълняват конкретни операции. На практика най-широко два етапа раздробяване.
Свързани статии